Metal 3D printing isn’t a new technology. It has shaped the field of rapid prototyping and manufacturing since the 1980s. However, in the last decade, companies offering this service experienced a huge uptick in projects requiring this manufacturing method.
One of the reasons there’s been a surge in demand for 3D metal printing in recent years is a shift in the rapid prototyping and manufacturing industry to avoid reliance on conventional manufacturing techniques, such as CNC machining.
We’ve seen a huge increase in investment in 3D metal printing technologies, resulting in the rapid advancement of the sector. Today, several options exist for 3D printing metal components with high-quality results.
This burgeoning industry trend in the manufacturing sector with the technology capable of producing parts in metallic composites, alloys, and metals. 3D metal printing allows manufacturers to create components of any desired chemical or mechanical properties.
This post unpacks 3D metal printing. We’ll look at how it works and the advantages of this process for rapid prototyping and manufacturing projects.
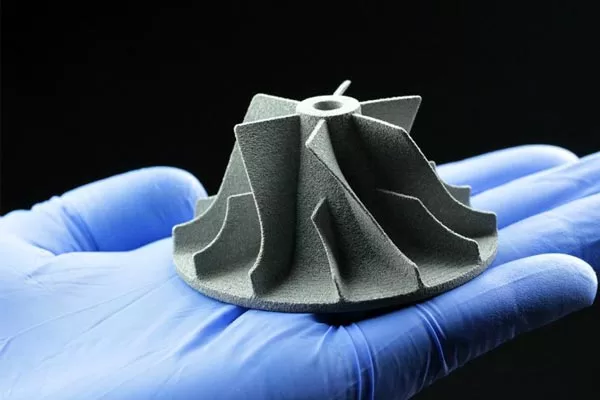
3d printing titanium alloy part
Metal 3D Printing Offers Huge Cost Savings
Across all manufacturing processes, project costs decline as production volume increases. Forming, casting, and machining are all examples of this cost reduction as economies of scale take hold with added volume.
We see cost savings with manufacturing because it reduces overhead for companies, lowering per-unit costs. Injection molding and casting are low-cost per unit/high-overhead manufacturing processes at low-volume production runs. In this instance, the distributed expense of molds drives up components costs to unmanageable levels.
However, the component cost becomes reasonable when produced in high volumes. Traditional fabrication methods have a high cost per part when manufactured at low volumes. In all manufacturing methods, the price per part drops as volume increases.
Metal 3D Printing offsets this cost conundrum with an automated process that incurs minimal overhead costs. There’s next to no difference in labor costs when we compare printing one part versus 100 parts.
The 3D printing system utilizes the same number of consumables on every part. The stability in cost per part doesn’t depend on the print volume. Therefore, it’s economical to use this process for manufacturing components in low volumes, such as for rapid prototyping projects.
However, it’s important to note metal 3D printing isn’t a cost-effective method for very high volumes. Most other manufacturing processes, such as casting and CNC machining, are more affordable, adding cost savings benefits for projects.
However, metal 3D printing offers a very affordable method to create prototype components for low to mid-volume production.
Here are some advantages of using metal 3D printing for your next rapid prototyping project.
Reduced Project Lead Times
3D metal printing, like all additive printing strategies, offers manufacturers a faster transition between the prototyping and production phases for components. Most of the time, savings come from instrumentation.
Typically, there’s no requirement for finishing or processing after printing components. The operator merely removes the support structures created during printing, and the part is ready to go. As a result, manufacturers and project managers see significant reductions in post-processing times.
There is no tooling the part using turning or milling to adjust the shape. There’s also no need for machining holes or connecting elements in the post-manufacturing process. So, project managers can expect a faster turnaround from manufacturers, with completion in days instead of weeks with conventional techniques.
For instance, using injection molding for component prototyping projects can take anywhere from 15 to 65 days to complete, whereas 3D metal printing finishes the job in a day or two. The result is a huge reduction in lead times and a faster transition to mass manufacturing.
3D Printers Are Ideal for Manufacturing Complex Components
All rapid prototyping and manufacturing methods have limitations, and 3D metal printing is no different. However, the unique process behind 3D printing allows for the fabrication of parts unsuitable for manufacturing using any other system.
This results in the optimization of parts for specific use cases rather than experiencing limitations with the constraints of conventional manufacturing processes. The components produced in 3D metal printing can be as complex as you like, such as topology-optimized components from design software or process-optimized components, such as injection molds with a customized manifold design or cooling.
These complex components may have design features like curves, cavities, or shapes where conventional systems can’t remove the material. However, 3D metal printing allows the production of these prototype parts without any post-production finishing.
In Closing
As industry continues with its mass adoption of 3D metal printing, we can expect to see new component design paradigms centering around the unique capabilities and strengths of 3D printing processes.
Metal 3D printing isn’t the end-all solution for rapid prototyping and manufacturing projects. It offers an alternate manufacturing method that opens opportunities previously unavailable due to cost concerns or design limitations.
It’s clear that metal 3D printing offers engineers and fabricators a new tool to add to their manufacturing and project processes, and they’ll continue to test the boundaries of this technology in the coming years.