Rapid tooling is frequently misunderstood in the manufacturing realm. It is no surprise as it is always used interchangeably with rapid prototyping.
Putting it simply, rapid tooling is when a conventional tooling practice and rapid prototyping techniques are used to create a part from CAD data. It allows for faster and more affordable production costs compared to traditional manufacturing techniques.
What are the Rapid Tooling Applications?
One of the most common applications of rapid tooling is when injection molding is used for rapid prototyping and low-volume manufacturing. In this manufacturing technique, the process can produce thousands of parts at a lower cost and much faster lead times. Some of the products made through injection molding include bottle caps, lego bricks, and medical syringes.
Conceptually, rapid tooling is any kind of injection mold tooling, manufactured quickly and inexpensively to test and validate parts before investing in production tooling. Although other prototyping options are available like 3D printing, CNC machining or vacuum casting are cheaper and faster in creating prototypes. This is one of the main advantages of rapid tooling.
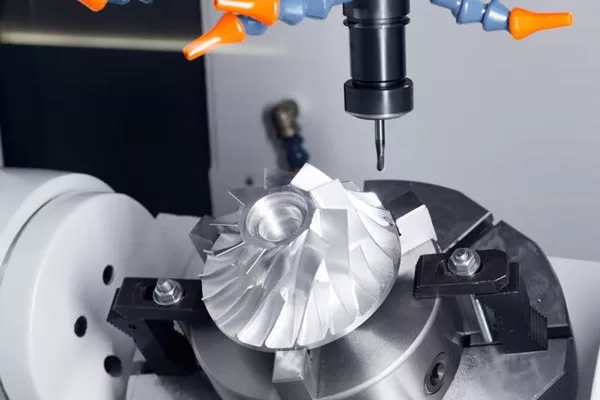
CNC machining
Benefits of Rapid Tooling
Rapid tooling can make high-quality prototypes that you can use to know how it will function in genuine applications. Aside from function, it will help the product designers to identify the correct material, leading to an even better final product. Here are the benefits of rapid tooling.
Opportunities for Innovation
Rapid tooling can open doors for innovations since it provides an opportunity for testing the form and function of a design before going to full production. Unlike traditional prototyping, the designers can create different versions of a single design. They can make models in different surfaces and shapes until they decide on the best option.
Efficiency
Regular prototyping would require a lot of time to create molds, models, and unique devices to turn a design into form. Rapid prototyping significantly minimizes the time between design and testing.
The outcome is a model that can be used for testing its structure, function, and ease of use. The product developer can revise the prototype based on the feedback of the customers since it is a semi-automated process. It gives organizations the upper hand because they can put up new items for sale in the market quickly.
Cost Savings
Another benefit of using rapid tooling is cost savings. Since product engineers can evaluate and test the prototype before going into final production, they can save money on the cost of tooling and materials.
They can detect the faults in the design and modify them before creating a hard tool or going into a full production run.
Conclusion
There are several reasons to choose rapid tooling aside from prototyping and testing. Because of rapid tooling, manufacturers can save on production costs and quickly get the products to market, making them suitable for low production runs.
Different companies have unique approaches to rapid tooling. But the nature of rapid tooling and product development process means companies like Nice Rapid can offer flexibility to achieve the requirements.