Do you want to get your products to market faster than your competition?
If yes, you need access to different rapid prototyping processes to manufacture the parts for testing and evaluation. The demand for faster and less expensive tooling solutions brought about several rapid tooling methods that were developed worldwide.
Rapid tooling has revolutionized prototyping since these new techniques were adapted in product development in recent times. This part of product development is a vast discipline and is quickly moving. These techniques combined rapid prototyping with conventional techniques to create a mold at a minimum time.
The rapid tooling techniques use a prototype model as a pattern to produce a mold or use other prototyping methods to fabricate a tool for a set number of parts. It is useful for low-volume parts where tooling costs can be expensive if we go through the usual route.
Types of Tooling
There are two types of rapid tooling techniques:
Direct Rapid Tooling – This type of tooling is used in the direct creation of molds. There is no requirement for any master pattern in direct rapid tooling. Some of the techniques employed are LENS, laminated tooling, direct AIM, quick casting method, and many more.
Indirect Rapid Tooling – This is the most common type of rapid tooling compared to direct tooling. Its purpose is more in prototyping and not in direct production. This type of rapid tooling is further divided into hard and soft tooling, which depends on the material used.
In choosing between the two options, you need to consider the purpose, volume, required precision, and the material used.
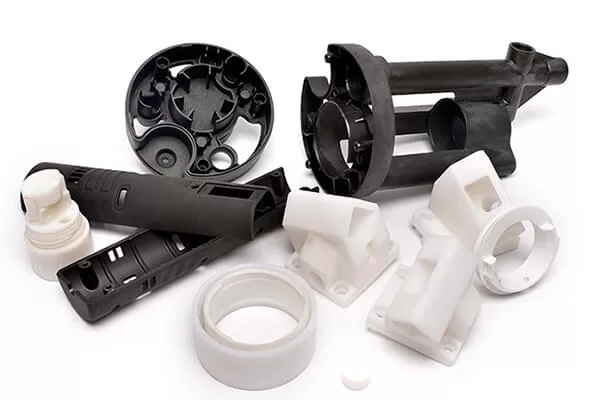
Plastic prototypes
Advantages of Rapid Tooling
In producing parts in low quantity, cost and lead-time are the most important points before deciding the technique to use. In general, the cost of the rapid tooling technique should not be more than one-fourth or one-fifth of the conventional method and below five percent of traditional tooling.
Rapid tooling creates prototypes that can be tested on their form and function. This allows for iterations during the early stages of development and thus, reducing the risk of errors in the final stages of production.
Other advantages of rapid tooling include:
- Reduce tooling time
- Allows the use of different materials
- Minimizes the cost of the entire manufacturing process
Challenges in Using Rapid Tooling
The only issue that manufacturers have with rapid tooling is its tool life. It is far shorter than conventional tooling. On the same note, the tools from RT have wider tolerances than those of traditional tools.
Conclusion
Rapid tooling uses a prototyping model as a pattern to form a mold in a short time. This is the answer for the demand during product development where samples are needed by product developers for functional testing. It serves as a bridge to final production, minimizing the chance of error along the way.
With rapid tooling, manufacturers benefit in producing a large number of thermoplastics and some thermosets and silicone through injection molding. The demand for cheap yet quick tools has brought about different rapid tooling techniques.