Developed in two German universities in the 1960s, silicone vacuum casting is a production technique which combines the two methods of duplication with vacuum and moulds of silicone. This duplication technique is widely employed for the manufacture of small batches of functional plastic components or end-use products or for producing the finest prototypes.
The materials used in this are silicone resin, of which the mould is made, and polyurethanes which is highly effective for mass production having the quality of mimicking the properties of materials. Silicone resin has heat the property of high heat resistance which is why it is a great material for moulding.
The procedure of vacuum casting
The first step in silicone vacuum casting is the creation of a model with the help of 3D printing, CNC machining or stereolithography. The model so created goes on to direct the creation of a silicone mould. Subsequently, the mould so produced is used to perform moulding employing the technique of vacuum injection with the help of a vacuum casting machine.
The process of vacuum casting is done by the injection of polyurethane resin into the silicone mould by the casting machine, which settles in the mould under applied heat. After one part gets cured, the mould can be removed and the same process can be reiterated a dozen times.
The reusability of silicone mould to produce more and more prototypes identical is of great value for small-scale and pre-series productions.
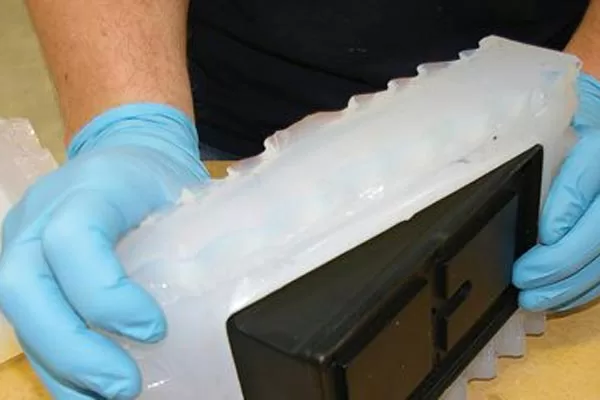
Vacuum casting services
How to get perfectly vacuum casted items?
There are some essentials, following which the process of vacuum casting can be enhanced to achieve the desired level of outputs. Some of them are discussed here.
Master model should be of high quality
The process of vacuum casting needs one to create an excellent quality master model. For this, the master model either be created using stereolithography or a high-quality industrial part itself can be used. The accuracy of the master model must be ensured to get error-free prototypes further.
High temperature
The curing process in silicone vacuum casting should be done under high temperature. This is to make sure that the material remains strong and durable.
Placing the mould in the vacuum chamber
As soon as you fill the resin material in the mould, make sure you place it in the vacuum chamber. This will guarantee that there will not be any air bubbles in the mould. The end product would thus be free of any damages or faults.
Mixing with metallic powder
The material that is designated to be filled in the mould if often mixed with some metallic power to add to its functional properties. The mixing powder will depend on the requirements from product to product.
Vacuum casting has many benefits over other methods like cost reduction, speedy work, high-quality, accuracy and production of detailed finished product. It is used in many industries for a large number of applications. With the above listed details in mind while carrying out the process of silicone vacuum casting, the final product of an optimum quality with all the benefits of vacuum casting could be obtained.