One of the most used manufacturing techniques to make high-volume parts is plastic injection molding. It is a method that relies on using a heated barrel and a particular mold with a cavity in creating different plastic products. It has various applications in different industries, and this article will explore the merits of using plastic injection molding.
The Benefits of Using Plastic Injection Molding
Many businesses prefer injection molding for various reasons. It is reliable and straightforward, but other benefits make plastic injection molding an excellent option for many projects. Here are some of them.
It is Efficient
Compared to other manufacturing processes, this method has a faster turnaround time. The molds are made according to the specification of the design, and its presses are programmed according to the requirements. All of these are easy to complete, and a single mold can create thousands of products. It is a more effective and more efficient fit for many progressive companies.
End Products are Consistent
One of the most appealing benefits of plastic injection molding is it can replicate products with consistency. Businesses rely on consistency to create brands, and injection molding provides them with consistent and reliable products, even if the orders are in large numbers. With this process, each product is as good as the next.
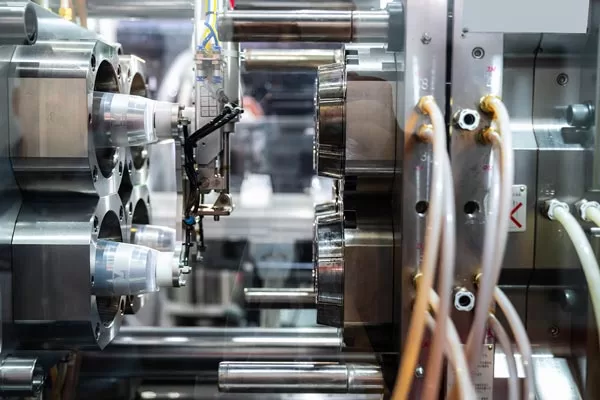
Plastic innjection molding machines
Simultaneous Use of Different Types of Plastic
Plastic injection molding does not rely on one type of material and instead accommodates different types of plastics. In the co-injection process, you can use multiple types of material in one product that fits its purpose. It can allow customization and gives the product its texture and strength.
Great Attention to Details
Products made from injection molding are durable. This is because they are exposed to extreme pressures compared with other manufacturing processes. You can have the design of complex geometries, and this process can still create these intricate parts.
Improved Strength
Plastic injection molding allows the addition of fillers in creating plastic parts. Fillers can reduce the density of the plastic during the molding process and provide additional strength to the end product. Any manufacturing process cannot duplicate this durability.
Cuts the Manufacturing Costs
The automated nature of plastic injection molding means that it operates on machines and robotics, thereby reducing the cost of production. It only needs to be supervised by an operator, which reduces back the overhead costs.
Because of automation, there is also less room for error as products are made accurately in one attempt preventing rejects and waste of raw materials through CAM (computer-aided manufacturing) and CAD (computer-aided design). The parts released from the mold have high-quality finish too, there is no need for further work.
Environment-Friendly
Despite what they say about plastic manufacturing, injection molding is more environment-friendly than other manufacturing processes. The plastic waste generated in the process can be recycled and reuse as raw materials and therefore leaving nothing for the landfills and dumpsites.