In producing plastic prototypes, the widely used technique is vacuum casting. Many have been using this process because it is economical, and experts recommend it for low to medium scale production. With this technique, it can produce copies of different functional plastic components. The entire process is quite fast than the other manufacturing methods. Also, the parts produced in are of high-quality and smoother finish.
The Process of Vacuum Casting
The vacuum casting process is a bit intensive, but you can still complete it in a faced-paced manner. Below are the stages of vacuum casting:
Producing the Master Model
The first step you need to do is to create the master model. The pattern could be an industrial part or done through 3D printing or CNC machining. The SLS technique produces the components through 3D printing. Make sure the master model used has the right dimensions so that the final casting parts will have the needed sizes.
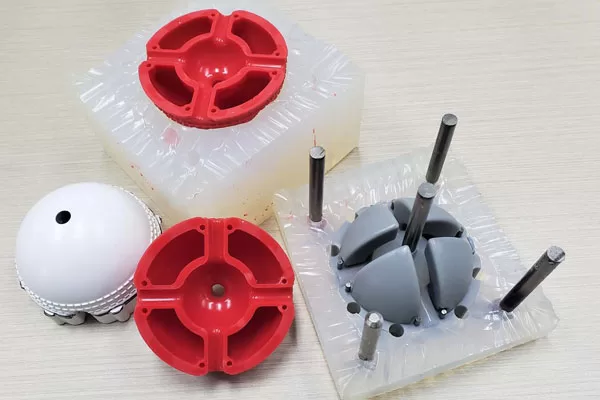
Vacuum casting products
Creating the Mold
To create a silicone mold, you need liquid silicone. As soon as you placed the master model inside the casting box, pour the liquid silicone on top of it and put it in the oven for curing. Open the cured liquid silicone, and remove the created master mold from the mold. The empty will have the same dimensions and shape as that of the original master pattern. You can use the mold 15 to 20 times.
Producing the Casting Copies
Adding the resins or polyurethane is the next step. It is a must that the mixture has the same properties as the actual part. Manufacturers keep a list of material data sheets that contains all the information about the properties and composition of the materials used for the process.
They use it as a reference to produce the resin that is similar to the properties of the main part. The mixture is added to the empty cavity to cast the product. It is then cured in a vacuum to ensure no bubbles are trapped.
The Casting Equipment
The casting equipment has two chambers. The top chamber has a pair of dies with a mold cavity in between them and a movable plate on top. In the cavity, you will find the vacuum.
The other chamber is the bottom chamber with a crucible. It collects the resin once it passes through a gating system. The system serves as a pathway in controlling the inflow of the resin. It is likewise utilized in collecting the resin in the crucible. Once the machine removed the excess material, the final casting product is ready.
Why Vacuum Casting?
As compared to rapid injection molding a popular technology used for the same type of manufacturing, vacuum casting has shorter lead times and cost less. The result of both processes is the same. If a small company or large industry needs to meet deadlines within a short time and intended for functional and prototype testing, vacuum casting is the best option depending on what you need.