Plastic injection molding features in a wide variety of manufacturing processes. From tiny components in medical devices to large machine housings, injection molding offers many production applications. Color consistency is a vital part of plastic injection molding and one of the most challenging aspects to control.
Mass production of plastic injection molded components can see swings in color consistency due to several factors. From variations in manufacturing processes to using different raw material batches, plenty of elements contribute to color variations in molded plastic components.
Common Causes of Color Inconsistencies in Plastic Injection Molding
- Pigments – Featuring manufacturing with titanium dioxide, pigments appear white in clear plastic. When exposed to UV light, the pigments partially absorb light and reflect the rest, producing various colors.
- Polymer Types – Different polymers feature unique colors, resulting in components with different hues than the expected color.
- Melt Temperatures – Miscalibration of the machine disrupts the uniformity of the resin as it melts. This problem produces issues like streaks or localized discoloration in final components.
- Plastic Resin Impurities – Contaminants like dust can create noticeable color differences.
How Manufacturers Can Control Color Consistency in Plastic Injection Molding
Plastic injection molding manufacturing processes can mitigate the risk of color differentiation and create consistency in final product colors by implementing the following procedures.
Remove Machine & Mold Errors
Manufacturers can create better color consistency in their final products by using an injection molding machine offering a similar capacity to the core product.
The machine could experience issues such as a dead corner, problems with the exhaust slot, or the mold pouring system. The manufacturer should replace their equipment with something suitable for the application.
Improve Control of Resin Raw Materials
Raw materials are frequently the culprit of issues with color consistency in plastic molded parts. Manufacturers shouldn’t ignore the importance of the thermal stability of resin on color fluctuations in finished products.
Most plastic injection molding manufacturers don’t produce raw material masterbatches in-house, relying on suppliers for their resin. Therefore, the manufacturer should implement tight qualify control measures on raw material inspections in production management.
Variations in suppliers of raw materials, especially when using different batches in a single production run, will lead to color inconsistencies.
Using the same supplier and brand for the masterbatch goes a long way toward improving color consistency. Manufacturers should always complete sample testing of raw materials before entering mass product production.
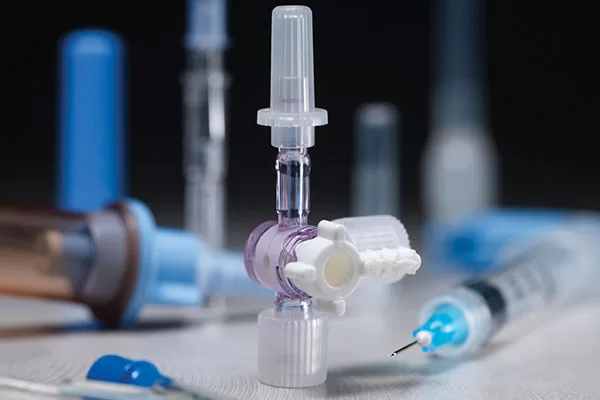
Plastic medical products
Ensure Proper Mixing of the Masterbatch
Improper masterbatch mixing between the plastic and color can result in color inconsistencies during production runs. After mechanically mixing the masterbatch, then feeding it into the machines hopper, the masterbatch separates due to an electrostatic effect on the material.
As a result, it absorbs easily on the wall of the hopper, changing the amount of masterbatch in an injection cycle.
This issue inevitably causes the masterbatch to change color properties in the injection cycle, creating color inconsistencies. Manufacturers can resolve this issue by adding the raw material to the hopper for manual mixing.
Efficient Regulation of Barrel Temperature
Incorrect heating of the raw materials due to damage or failure of the heating ring or dramatic swings in the temperature of the heating barrel will lead to color inconsistencies. Manufacturers should ensure effective, efficient heating for color consistency.
Proper Adjustment of Process Parameters
Manufacturers should avoid using high back pressure, high injection speeds, and other processes involved in the injection molding process that cause a shearing effect.
Thermal degradation of materials or localized overheating are common factors in creating color inconsistencies. Manufacturers must pay attention to the temperature in each barrel section, especially close to the nozzle.