Material performance is significant in any application, even more so when the lives and health are at stake. One of the particular challenges in finding a material that is viable for medical application is tough enough to withstand heat, chemical exposure, and pressure but also comfortable for the patient. Not many materials have these characteristics until liquid silicone rubber.
The liquid silicone rubber molding process is not new. It has been around for years, and with the technological advances added, it has become significant in manufacturing medical devices and wearables. Liquid silicone rubber cures faster and offers unique properties that conventional rubber materials are what makes it vital in producing medical items with ease.
Unique Properties of Liquid Silicone Rubber
The basic material in liquid silicone rubber molding is, of course, silicone rubber. It is made from silicon dioxide that is processed into pure silicone. When combined with methyl chloride through a series of processes, it can turn into different forms, including liquid.
Liquid silicone rubber is a reactive chemical with a thick, similar to a paste consistency, like peanut butter. It comes in two components, usually in separate containers, and mixed in a 1:1 ratio to create a reaction. When applied with heat, these two separate liquids will combine to form rubber.
The liquid silicone molding process is a clean production technique since it occurs in a closed system. There is no ambient air that reacts with the parts when they are removed from the mold. Hence it is free from moisture and dust. This clean production condition improves the quality of the parts, as there are no contaminants that can affect the physical properties of the rubber material.
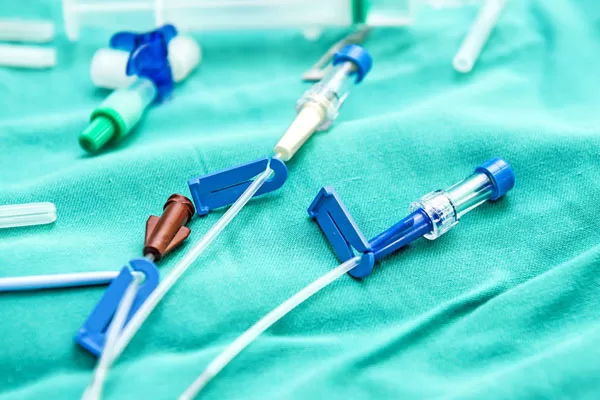
Silicone medical devices
Medical Applications of Liquid Silicone Rubber
The use of liquid silicone rubber is expanding. Aside from the traditional rubber applications, where rubber materials have never been used before, it is now used in home goods, industrial and automotive applications, wearables, and medical devices.
The most common use of LSR is in medical devices. Since LSR cures completely and quickly, it answers the need for a material that does not leach chemicals and cause harmful reactions with the patient’s body. Latex, another material used in the material industry, does not fully cure during manufacturing and can have adverse reactions with patients.
Since the chemical components of LSR do not disintegrate when subjected to high temperatures, it can handle sterilization. This unique property of this material contributes to its effectiveness for use in medical and even baby care.
Finally, the most critical advantage is the ability to use LSR in drug-eluting devices (DEDs). An example of this is in contraceptive products and pacemaker catheter leads. By including LSR, it enables the leads to introduce the anti-inflammatory medication directly into the heart tissue.
Conclusion
Liquid silicone rubber continues to provide more effective solutions to replace the existing old technologies. With improved production techniques and improvements on the material itself, it will most likely replace traditional rubber used in many industries. The key to its success is in the production process. The advancements in liquid silicone rubber molding technology will take full advantage of LSR’s full potential.