The manufacturing process has become easier now more than ever, this is partly thanks to the changing trends in technology which has come up with innovative technology and techniques to keep up with the ever-changing needs and preferences of clients.
One of the most innovative production techniques is compression molding, if you are looking to cut down on overall production cost as well as reduce material wastage then this is the perfect technique for you.
For beginners, you might be wondering what is this type of production technique? Well, worry no more, for this post we are going to discuss everything regarding compression molding.
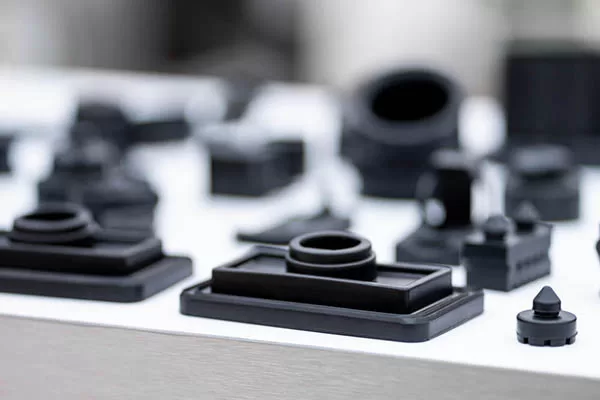
Compression molding products
Materials used in compression molding
Both thermosets and thermoplastics are used in compression molding, thermoplastics is a type of plastic material that is pliable and soft when heated and becomes hard when its cooled while thermoplastics can be heated and cooled multiple times according to your design and preference.
Thermosets materials comprise polymers and plastics that will become cured when they are exposed to heat. What this essentially means they can be shaped or molded once. Compression molding will cause the thermosets to completely transform a chemical way in a manner that can’t be repeated or undone.
Some of the most common materials used in compression molding include:
- Diallyl phthalate (DAP)
- Epoxy
- High-density polyethylene (HDPE)
- Melamine
- Polyamide-imides (PAIs)
- Polyether ether ketone (PEEK)
- Polyurethane (PU)
- Polyphenylene sulfide (PPS)
- Phenolic resins (PF)
- Polytetrafluoroethylene (PTFE)
- Silicone
- Urea-formaldehyde (UF)
- Urethane
How molds are created using compression molding?
The type or model of creation is solely dependent on the charge or material that will be used in compression molding. This is good news for both manufacturers and clients as you’ll have a wide variety of options when it comes to the creations of the molds.
One of the key features is the fact that your mold should be able to withstand all the pressure and heat that comes with compression molding.
Die casting
Die casting is amongst one of the best ways to create molds used in compression molding, this is the go-to technique as it will create durable metal parts with a cost-effective budget in comparison to other production techniques.
However, you should always keep in mind that dies created form the die casting process is mainly created using CNC machining. Both die casting and CNC machining go hand-in-hand
CNC machining
CNC machining is also another viable way of creating detailed and comprehensive compression molds. The automation and computerization part of CNC machines will give both engineers and designers more control over the design phase.
But, the catch with compression molding is it’s a bit expensive. To cut down on cost, manufacturers always opt to use both die casting and CNC machining, this will allows you to create molds cost-effectively.
3D printing
Tooling molds can also be created using 3D printing, if you looking to prototype limited and smaller parts then 3D printing is the perfect solution. It’s one of the cheapest and fastest ways of creating molds
Where heatless applications are involved, 3D printing is the most widely used technique when it comes to making compression molds.