Compression molding remains a procedure that is commonly used for thermoset and thermoplastic materials. For this process to be successful, it’s crucial to position plastic items into a cavity that is structured by pressure and heat. If you have experienced the making of waffles, then compression molding will not be difficult to understand. In every section of the mold, you’ll discover that pressure and heat make materials to spread.
Through the pressure and heat cycle, the material becomes hardened and later removed. To create the end product, it’s important to make use of different layers of various reinforcement items on thermosetting materials such as melamines, phenolics, polyesters, and other resin compounds in a compression mold. Studies have shown that several thermoplastic items that get compression molded to get better results.
The Essence of Performing Compression Molding:
When talking about this production procedure, you can always think of something like injection molding. With cavities and machined aluminum or steel tools, the process will become a reality by pouring material parts that help to create the end product. In this process, fluorosilicone and rubbers are crucial materials that experts use. In compression molding, there is no need for materials being converted into the liquid state and poured via the gate.
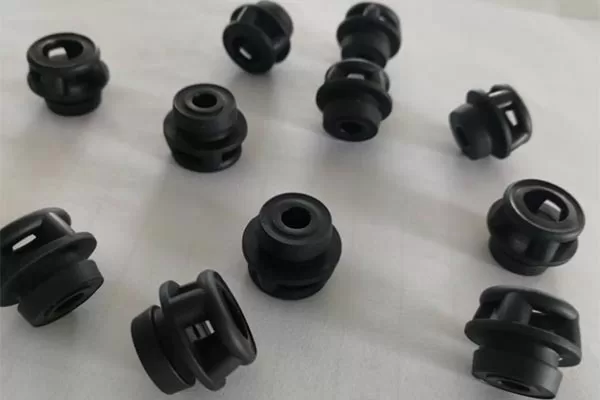
Compression molding parts
The tool cavity will have to contain pre-heated items and broken down to create designs through a vertical press procedure. It’s always cheaper to get tools that people can use to compress materials in this process. The process also involves gating, ejection, and parting. Creating a whole new product is the goal of adopting this production process.
Disadvantages of Using This Manufacturing Procedure:
- In the comparison of thermoplastics, the price may be higher than several extruded products,
- There is plenty of slow cycle times that can affect production for more items,
- The flask process may need you to pass through trimming.
Advantages of Using Compression Molding:
- The cost of buying tools is cheap,
- Producing massive parts is possible at a cheap cost,
- When materials are in stock shape, there is zero or no residue stress.
The Process of Compression Molding:
Wherever there is a fit, you can always count on the advantages of compression molding. While the procedure remains primary in most cases, it can always be used to create base stock designs in thermoplastics. Using this process in production will help in machining tough geometrics without any stress. Compression molding remains a manufacturing procedure that does not consume time. While lowering the overall amount of manufacturing, the process can also help in boosting production. The truth is that compression molding is the pathway for producing top-notch parts.
If you’re looking for a reliable way to make cheap silicone and rubber parts, then give this production technology a try. Instead of using undercuts, industry experts can rely on this manufacturing style for designing geometries. For instance, if you want to design footwear, gaskets, phone cases, or even bellows, using this production process can help. Another thing to know about this process is that it will not cause sick deformation, shrinkage, or warping.