Silicone molding stands as a cornerstone of modern manufacturing, offering unparalleled versatility and precision across a spectrum of industries. From creating intricate prototypes to producing high-volume consumer goods, silicone molding has become a go-to solution for manufacturers seeking cost-effective, efficient, and high-quality production methods. Let’s delve into the world of silicone molding to understand its workings, applications, and transformative impact on diverse sectors.
Understanding Silicone Molding
At its core, silicone molding involves the use of silicone rubber to create molds that faithfully replicate the details of an original master pattern. These molds can then be used to produce multiple copies of the original object, ensuring consistency and precision in the final output. The process typically involves several steps:
- Master Pattern Creation: The process begins with the creation of a master pattern, which can be made from various materials such as wood, plastic, or metal. This pattern serves as the template for the final product and must be meticulously crafted to capture all the desired details.
- Mold Making: Once the master pattern is ready, a mold is created around it using liquid silicone rubber. This silicone material is poured or injected around the pattern, where it cures to form a flexible and durable mold that faithfully replicates its contours.
- Casting: With the mold in hand, manufacturers can now begin the casting process. This involves pouring or injecting the desired material, such as plastic, resin, or rubber, into the mold cavity.
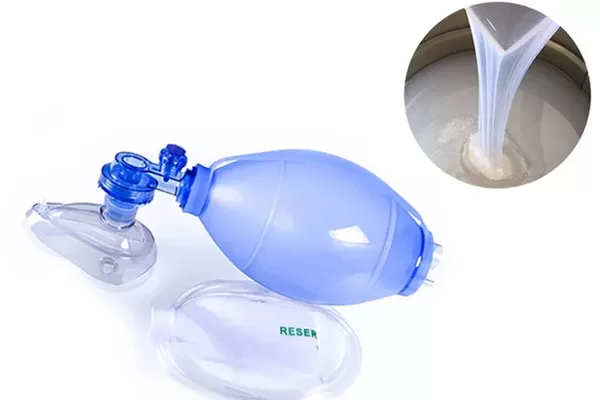
Medical lsr devices
Applications Across Industries
The versatility of silicone molding lends itself to a myriad of applications across diverse industries:
Prototyping: Silicone molding enables rapid prototyping by allowing designers and engineers to quickly create multiple iterations of a product for testing and validation. Its ability to reproduce intricate details makes it ideal for prototyping complex components and assemblies.
Consumer Goods: From kitchen gadgets to phone cases, silicone molding is widely used in the production of consumer goods. Its flexibility, durability, and resistance to heat and chemicals make it well-suited for applications where safety, comfort, and longevity are paramount.
Medical Devices: In the medical industry, silicone molding plays a critical role in the production of devices such as prosthetics, catheters, and surgical instruments. Its biocompatibility, sterilize ability, and flexibility make it an ideal material for applications requiring precision and reliability.
Automotive Components: Silicone molding is employed in the automotive industry to produce a wide range of components, including gaskets, seals, and interior trim. Its ability to withstand extreme temperatures and harsh environments makes it a preferred choice for automotive applications.
Electronics: Silicone molding is used in the manufacturing of electronic devices and components, such as keypads, connectors, and encapsulation for circuitry. Its electrical insulation properties, along with its resistance to moisture and corrosion, make it indispensable in the electronics industry.
In conclusion, silicone molding stands as a versatile and indispensable manufacturing technique, driving innovation across a wide range of industries. Its ability to produce high-quality parts with precision, speed, and cost-effectiveness makes it a preferred choice for manufacturers seeking to stay competitive in today’s dynamic marketplace. As technology continues to evolve and new materials and processes emerge, the potential for silicone molding to reshape the future of manufacturing is limitless.