For those new to the aluminum extrusion process, let this article show you how it is done.
Have you ever played with Play-Doh and the Shape Maker when you were a kid? Well, the aluminum extrusion process works in the same way. When the molten aluminum material is pressed through the opening that is fitted with a specific die shape, it looks like the Play-Doh coming out of the plastic device.
Fitting this opening with a hollow die shape, like in a Play-Doh Shape Maker, will have the material taking shape as it comes out of the opening. You can see the part of the die that forms the outside diameter and the inside with two supports. As it comes out, the Play-Doh separates into two halves and welds back together because of the pressure that makes it flow through the opening of the tubular shape.
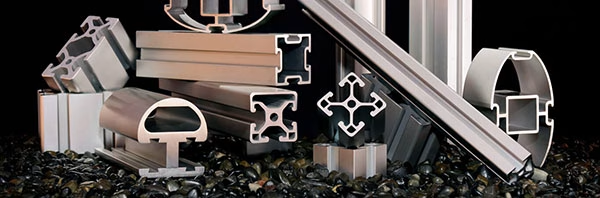
Custom extruded aluminum
More than a Child’s Play
The aluminum extrusion process is, of course, more complicated than creating something out of Play-Doh. But the process is similar but a little different. It uses a powerful hydraulic press in producing a wide range of useful products in any shape imaginable made possible by aluminum extrusion.
The process begins with choosing the desired shape for the finished product and the appropriate aluminum alloy to be used. Aside from these two, the extrusion die and the associated tooling is also prepared.
The most common form of aluminum alloy is in the billet. It is described as a log of extrusion feedstock. This and the tooling are both preheated. The process begins when the press ram begins applying pressure to the billet inside the container.
The hydraulic presses can exert pressure ranging from 100 to 15,000 tons. The pressure capacity of hydraulic presses will determine the dimension of the extruded materials. Aluminum has a melting point of 1,220 degrees Fahrenheit, and in extrusion operations, the temperature requirement is above 700 degrees Fahrenheit to as high as 930 degrees Fahrenheit.
Once the pressure is applied, the aluminum billet is crushed against the die. It will become shorter and wider but the expansion will be restricted to the confined walls. As the pressure increases, the soft but still solid material will have no place to go and will begin to squeeze out passing through the shaped die. When it emerges it will have a fully formed profile.
The extruded material is cut off from the remainder of the metal while the remainder will be recycled into new material. Once it leaves the die, finishing processes like quenching, mechanical treatment, and aging will ensue. This process will impart the metallurgical and physical properties to the product.
Once the extruded metal finishes the aging process, either at the oven or room temperature, it will be moved to another section for further processes like anodizing and fabrication, depending on the product specifications.
Benefits of Aluminum Extrusion Products
Aluminum extruded materials have plenty of advantages over other metal products. Although these metals can match or be superior to aluminum in properties they cannot have the characteristics of aluminum at once.
Included in these advantages are:
- Lightweight: Aluminum is only one-third of the weight of metals iron, brass, or copper. That is the reason why it is more economical to use in aerospace, automotive, and construction.
- Strong: When it comes to strength, aluminum is strong enough to accommodate different temperatures. It is even stronger in colder temperatures.
- Corrosion-resistant: Aluminum is resistant to rust as its surface is protected with a film of oxide. This property is further enhanced during anodizing.
- Excellent Thermal Conductivity: Aluminum can conduct heat better than most metals. As such, it is a great heat exchanger. Extruded materials are often used for thermal conduction.
- Affordable: Since the extrusion process is more straightforward, it is less expensive. It can be used as an affordable prototyping technique.
Conclusion
As you can see, the aluminum extrusion process is easy to understand. All you need is a reliable partner to execute your concept with aluminum extrusion.