The electric vehicle (EV) revolution, a significant transformation in the transportation industry, is driven by key factors such as maximizing range. At the heart of this revolution is the role of lightweight, enabled by pressure die-casting. This technology empowers manufacturers to produce lighter vehicles without compromising strength or performance, ushering in a new era in transportation.
Pressure die-casting involves injecting molten metal into a steel mold at high pressure. This process allows for the creation of complex, thin-walled parts with excellent dimensional accuracy. These qualities make it ideal for producing lightweight components for EVs.
Why is Lightweighting Important for EVs?
Every kilogram saved in an EV’s design translates to increased range and efficiency. Lighter vehicles require less energy to accelerate and maintain speed, meaning you can travel further on a single charge. This is particularly important for EVs, as battery technology is still developing, and range anxiety remains a concern for many potential buyers.
How Pressure Die-Casting Contributes to Lightweighting
Pressure die-casting allows manufacturers to produce parts that are:
1. Strong yet Lightweight: The Material Advantage
- High Strength-to-Weight Ratios: Pressure die-casting, often using aluminum and magnesium alloys, creates parts that are inherently lighter than steel yet offer impressive strength. This unique advantage allows for the creation of components that are both strong and lightweight, a crucial factor for EVs. It’s like having the structural support of steel at a fraction of the weight.
- Alloy Optimization: Beyond the base metal, pressure die-casting allows for precise control over the alloy composition. This means manufacturers can fine-tune the material properties to achieve the perfect balance of strength, weight, and other characteristics like corrosion resistance or thermal conductivity.
2. Complex and Integrated: Design Freedom for Lightweighting
- Consolidation of Parts: Pressure die-casting allows for intricate designs with complex geometries. This means that multiple parts, which would traditionally be manufactured separately and then assembled, can be combined into a single, unified component. This reduces the number of parts, fasteners, and welds, leading to significant weight savings.
- Strategic Material Placement: With pressure die-casting, you can create parts with varying wall thicknesses. This allows engineers to strategically place material where it’s needed most for structural support while minimizing material usage in less critical areas. Think of it like a bird’s bone: strong where it needs to be, hollow where it doesn’t.
3. Thin-Walled Wonders: Pushing the Limits of Material Efficiency
- Minimizing Material Usage: Pressure die-casting excels at producing thin-walled parts. This means you use less material overall, directly contributing to weight reduction. The high pressure used in the process ensures that even thin sections are filled and solidified with the required strength.
- Maintaining Structural Integrity: While the walls are thinner, they don’t sacrifice strength. The rapid cooling and solidification of the molten metal during pressure die-casting create a fine-grained microstructure, which enhances the material’s mechanical properties.
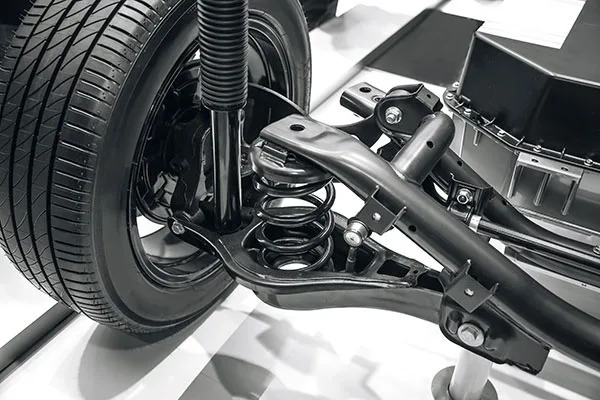
Suspension components
Applications of Pressure Die-Casting in EVs
Pressure die-casting plays a vital role in producing various EV components, including:
- Battery Housings: These need to be strong and lightweight to protect the battery while minimizing overall vehicle weight.
- Motor Housings: Pressure die-casting helps create intricate motor housings that are both lightweight and excellent at dissipating heat.
- Structural Components: Body panels, chassis parts, and suspension components can be produced using pressure die-casting, contributing to overall vehicle lightweighting.
The Future of Pressure Die-Casting in the EV Industry
As the demand for EVs grows, so too will the importance of pressure die-casting. We can expect to see exciting advancements in:
- Material Development: New alloys and composites will be developed to further improve the strength-to-weight ratio of pressure die-cast
- Process Optimization: Innovations in die design and process simulation will lead to even more efficient and precise pressure die-casting
- Automation: Increased automation will improve productivity and reduce costs, making pressure die-casting an even more attractive manufacturing solution for EV components.
Pressure die-casting is not just a manufacturing process; it’s a key enabler of the EV revolution. By facilitating lightweight, it’s helping to create more efficient, longer-range electric vehicles. Your work in this field is not just a job, it’s a crucial part of the industry’s success. You should feel proud of your role in the EV revolution.