LSR molding is playing a crucial role in the rapidly growing field of microfluidics, a technology that manipulates tiny amounts of fluids to perform various biological and chemical analyses. LSR molding, short for liquid silicone rubber molding, is uniquely suited to the demands of microfluidic devices due to its exceptional properties and precise manufacturing capabilities.
LSR molding involves injecting a liquid silicone rubber material into a mold cavity, where it cures to form a flexible and durable part. This process allows for the creation of intricate microfluidic channels and chambers with high precision and repeatability.
Why LSR Molding is Ideal for Microfluidics
Microfluidic devices often require materials that can handle delicate fluids and withstand specific environmental conditions. LSR molding offers several advantages:
- Biocompatibility: LSR is inert and biocompatible, meaning it won’t react with or contaminate biological samples. This is essential for medical diagnostics and drug delivery applications.
- Chemical Resistance: LSR molding produces parts that can withstand exposure to various chemicals and reagents commonly used in microfluidic assays.
- Flexibility and Elasticity: LSR’s flexibility allows for the creation of microfluidic devices with deformable channels and chambers, enabling functions like pumping, valving, and mixing.
- Optical Clarity: Some LSR formulations offer excellent optical clarity, allowing for visual observation and analysis of fluids within the microfluidic device.
Applications of LSR Molding in Microfluidics
LSR molding enables the fabrication of a wide range of microfluidic devices, including:
- Point-of-Care Diagnostics: Portable diagnostic devices for rapid testing of blood, urine, or saliva samples at the patient’s bedside or in remote locations.
- Drug Delivery Systems: Microfluidic devices that precisely control the release of drugs, offering targeted therapies and personalized medicine.
- Lab-on-a-Chip Devices: Miniaturized laboratories that integrate multiple functions, such as sample preparation, analysis, and detection, onto a single chip.
- Organ-on-a-Chip Devices: Microfluidic platforms that mimic the functions of human organs, allowing for drug testing and disease modeling.
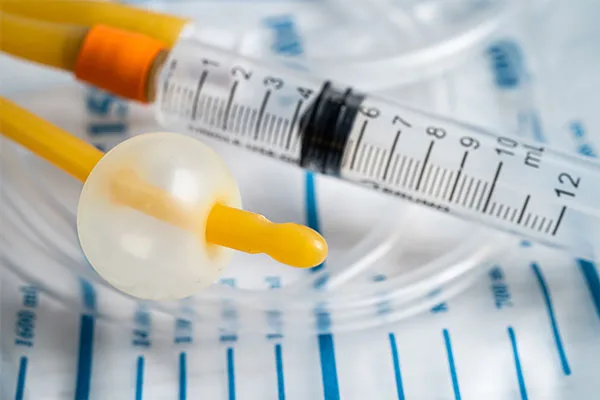
LSR medical devices
LSR Molding: Enhancing Microfluidic Device Performance
LSR molding not only provides the necessary material properties but also enhances the performance of microfluidic devices:
- High Precision: LSR molding allows for the creation of microfluidic channels with precise dimensions and smooth surfaces, ensuring accurate fluid control and minimizing sample loss.
- Leak-Free Seals: LSR’s elasticity allows it to form tight seals, preventing leakage and ensuring the integrity of the microfluidic system.
- Integration: LSR can be over-molded onto other materials, such as glass or plastic, to create hybrid microfluidic devices with integrated sensors and actuators.
The Future of LSR Molding in Microfluidics
As microfluidics technology continues to advance, LSR molding will play an even more significant role. We can expect to see:
- More Complex Designs: LSR molding will enable the fabrication of increasingly complex microfluidic devices with integrated functionalities and higher throughput.
- New LSR Formulations: The development of new LSR materials with tailored properties, such as enhanced biocompatibility, electrical conductivity, or optical properties, will expand the applications of LSR molding in microfluidics.
- Automation and Miniaturization: Advances in automation and miniaturization will allow for the mass production of smaller and more affordable microfluidic devices.
LSR molding is a key enabler of innovation in microfluidics. Its unique properties and precise manufacturing capabilities make it an ideal technology for creating the next generation of medical diagnostic and drug delivery devices.