Pressure die casting, a metal casting process that involves injecting molten metal into a steel die under high pressure, is a versatile technique that consistently delivers precise, high-quality parts with excellent surface finishes. This reliability is a testament to the robustness of the process.
While the fundamentals of pressure die casting remain consistent, the industry is constantly evolving to improve efficiency, sustainability, and the capabilities of the process. Let’s explore some of the latest advancements and trends.
High-Pressure Die Casting: Achieving Complex Geometries
Pressure die casting is known for its ability to create complex shapes and intricate details. Advancements in die design and casting technology are pushing the boundaries of what’s possible. Think thin walls, intricate internal passages, and tight tolerances.
These advancements are driven by:
- Improved Die Materials: Using high-strength steel alloys allows for more complex die designs and longer die life.
- Simulation Software: Sophisticated software helps engineers optimize die design and casting parameters to ensure high-quality results.
- High-Speed Injection: Injecting molten metal at higher speeds allows for better filling of intricate cavities.
With these advancements, pressure die casting can produce parts with greater complexity and precision than ever before.
Vacuum Die Casting: Enhancing Quality and Reducing Defects
Vacuum pressure die casting is a specialized process that involves creating a vacuum within the die cavity during injection. This technique offers several advantages:
- Reduced Porosity: The vacuum helps to remove air and gas from the molten metal, resulting in parts with fewer pores and improved structural integrity.
- Improved Surface Finish: Vacuum die casting can produce parts with smoother surfaces and better cosmetic appearance.
- Thinner Walls: The vacuum assists in filling thin-walled sections, expanding design possibilities.
By minimizing defects and enhancing quality, vacuum pressure die casting is ideal for applications where structural integrity and surface finish are critical.
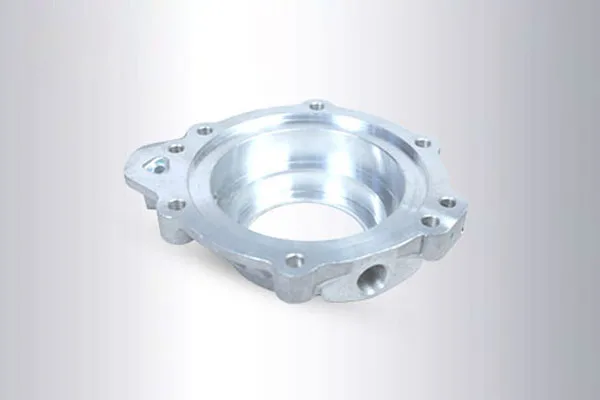
Pressure die casting automotive parts
Pressure Die Casting with Magnesium Alloys: Lightweighting for the Future
Magnesium alloys are gaining popularity in pressure die casting due to their exceptional strength-to-weight ratio. These lightweight materials are crucial in industries like automotive and aerospace, where reducing weight is a key objective.
Benefits of magnesium in pressure die casting:
- Lightweight Components: Magnesium is significantly lighter than aluminum and zinc, making it ideal for lightweight applications.
- Excellent Strength: Despite its low weight, magnesium offers good strength and stiffness.
- Good Castability: Magnesium alloys flow well and fill intricate die cavities effectively.
As the demand for lightweight and fuel-efficient products grows, pressure die casting with magnesium alloys will play an increasingly important role.
Automation and Industry 4.0 Revolutionizing Pressure Die Casting
The pressure die casting industry is undergoing a transformation with the adoption of automation and Industry 4.0 technologies. These advancements are enhancing efficiency and productivity, and reshaping the way pressure die casting is performed.
Pressure die casting is not just embracing, but thriving with automation and Industry 4.0 technologies. These advancements are not just enhancing efficiency and productivity, but also shaping the future of the industry, making it an exciting time to be part of this field.
Here’s how:
- Robotic Automation: Robots are used for tasks like die loading, part extraction, and trimming, improving speed and consistency.
- Real-time Monitoring: Sensors and data analytics provide real-time insights into the casting process, allowing for adjustments and optimization.
- Predictive Maintenance: AI algorithms can predict when maintenance is needed, minimizing downtime and maximizing productivity.
By integrating automation and Industry 4.0 principles, pressure die-casting operations can achieve higher levels of efficiency and competitiveness.
Sustainability in Pressure Die Casting
The pressure die-casting industry is not just focused, but committed to sustainability. Efforts such as energy efficiency, recycling, and process optimization are not just initiatives, but a responsibility we all share in creating a more environmentally responsible manufacturing sector.
- Energy Efficiency: Implementing energy-efficient equipment and processes to reduce energy consumption.
- Recycling: Recycling scrap metal and die materials to minimize waste and environmental impact.
- Process Optimization: Optimizing casting parameters to reduce material usage and scrap generation.
By adopting sustainable practices, pressure die casting can contribute to a more environmentally responsible manufacturing sector.
Pressure die casting is a dynamic and evolving technology. By staying informed about the latest advancements and trends, you can leverage this process to create high-quality, innovative, and sustainable products.