Remember those plastic building blocks you played with as a kid? Or that cool action figure? Chances are, they were made with plastic injection molding. It’s a process that’s been around for ages, but trust me, it’s not your grandpa’s manufacturing anymore! Thanks to Industry 4.0, plastic injection molding is getting a serious tech upgrade. Think smarter factories, lightning-fast production, and a whole lot less waste. Let’s dive in!
Robots are Taking Over (But in a Good Way!)
Okay, maybe “taking over” is a bit dramatic. But robots are playing a bigger role in plastic injection molding these days. And that’s a good thing! Robots are great at repetitive tasks, like pulling out finished parts or loading materials. This not only speeds up the production process but also frees up human workers to focus on more complex jobs, like troubleshooting and quality control, ensuring their roles remain crucial in the manufacturing process.
But it’s not just about robots. Artificial intelligence (AI) is also making a huge impact. Imagine an AI that can predict when a machine needs maintenance before it breaks down. That’s exactly what’s happening in smart factories. More importantly, AI is being used to fine-tune the plastic injection molding process in real time, ensuring we consistently produce better quality parts with less waste, giving us confidence in the products we manufacture.
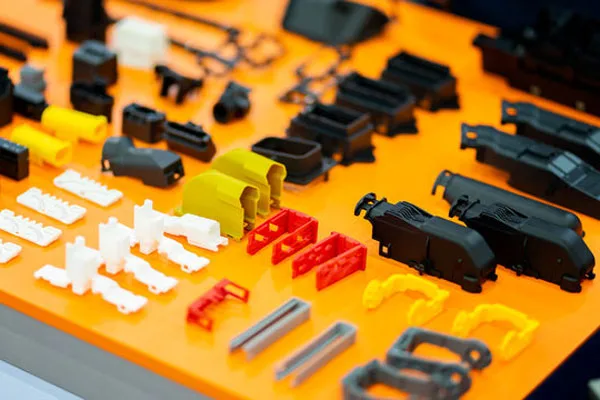
Plastic parts
Eco-Friendly Plastics? You Got It!
You probably know that plastic waste is a big problem. But the good news is that the plastic injection molding industry is stepping up its game. We’re seeing more and more companies using recycled plastics and bioplastics.
Bioplastics are made from plants, like corn or sugarcane, instead of oil. Pretty cool. And using recycled plastics means less waste ends up in landfills. That plastic water bottle you recycle might come back as a cool new gadget thanks to plastic injection molding.
3D Printing: The Mold Maker’s New Best Friend
Remember when making a mold for plastic injection molding was a long and expensive process? Well, not anymore! 3D printing is changing the game. Now, we can print molds quickly and cheaply, which is perfect for testing out new designs or making small batches of specialized parts.
This is a game-changer for inventors and small businesses. They can use 3D-printed molds to create prototypes and test their ideas without breaking the bank. And if they only need a few hundred parts, they can even use 3D-printed molds for production, reducing costs and making their businesses more sustainable.
The advantages of 3d printing for plastic injection molding as follow:
- Faster Prototyping: 3D printing enables quick prototype creation, speeding up design and testing before committing to costly injection molds.
- Lower Costs: Eliminates expensive tooling and mold creation, making it cost-effective for prototyping and small batch production.
- Complex Geometries: Allows for intricate designs and features (like internal channels or undercuts) that may be difficult with traditional molding.
- Short-Run Production: Ideal for low-volume or custom parts, bypassing the need for expensive molds in small quantities.
- Tooling Optimization: 3D-printed molds or parts can be tested and refined, reducing errors in final mold production.
- Material Flexibility: Use of similar materials for prototyping and testing, and easy experimentation with different materials.
- Lower Risk in Design: Quickly test and adjust designs, minimizing the risk of costly errors in mold-making.
- Environmental Benefits: More material-efficient than traditional molding, reducing waste and offering options for sustainable materials.
- Customization: Perfect for producing customized or unique parts in small quantities without custom molds.
- Faster Time to Market: Rapid prototyping and design iteration speeds up the overall product development cycle.
Simulation Software: No More Guesswork
Before we even start injecting plastic, we can use super-smart software to simulate the whole process. This helps us see how the plastic will flow through the mold and identify any potential problems. It’s like having a crystal ball for plastic injection molding!
This simulation software helps us design better molds and avoid costly mistakes. It’s all about getting it right the first time so we can make high-quality parts efficiently.
Plastic injection molding is definitely keeping up with the times. With all these advancements, we can expect even more amazing and sustainable plastic products in the future. Who knows what cool things we’ll be molding next?