The electric vehicle (EV) industry is rapidly expanding, and with it, the demand for high-performance batteries. At the heart of this growth is compression molding, a manufacturing process that plays a critical role in producing key components for these batteries, making you an integral part of this industry’s progress?
Compression molding involves placing a preheated material into a mold cavity and then applying pressure to shape it. This process is well-suited for creating complex parts with tight tolerances and excellent dimensional stability, making it ideal for EV battery applications.
Why Compression Molding is Essential for EV Battery Production
EV batteries require components that can withstand harsh conditions, including high temperatures, vibration, and exposure to chemicals. Compression molding offers several advantages that meet these demands:
- High-Strength Materials: Compression molding can process a wide range of materials, including advanced composites and thermoset plastics. These materials offer excellent strength, stiffness, and resistance to heat and chemicals, making them ideal for battery components.
- With compression molding, you can rest assured that the finished parts will have precise dimensions and tolerances, a crucial factor for battery components that require accurate fit and alignment, ensuring the quality of EV battery components.
- Complex Geometries: The process can create parts with complex shapes and intricate features, which is often necessary for battery housings, separators, and other components.
Applications of Compression Molding in EV Batteries
Compression molding is used to produce various EV battery components, including:
- Battery Cases and Housings: These provide structural support and protection for the battery cells.
- Battery Pack Covers and Seals: These help to prevent moisture and contaminants from entering the battery pack.
- Insulators and Separators: These electrically isolate the battery cells and prevent short circuits.
- Thermal Management Components: These help regulate the temperature of the battery pack, improving its performance and lifespan.
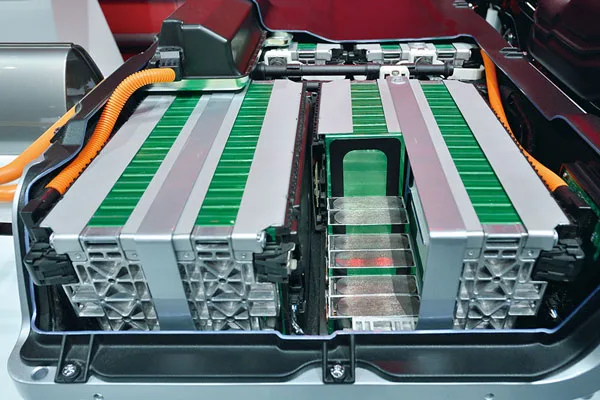
Electric vehicle batteries
Compression Molding: Enhancing EV Battery Performance
Compression molding not only produces durable and reliable components but also contributes to improved battery performance:
- Lightweighting: By using lightweight materials and optimizing part design, compression molding can help reduce the overall weight of the battery pack, improving vehicle efficiency.
- Thermal Conductivity: Compression molding can be used to create components with high thermal conductivity, which helps to dissipate heat and prevent thermal runaway in the battery pack.
- Electrical Insulation: The process can produce components with excellent electrical insulation properties, ensuring the safe operation of the battery pack.
The Future of Compression Molding in the EV Battery Industry
As the EV market continues to grow, compression molding will play an increasingly important role in battery production. The future holds exciting advancements, such as new materials and increased automation that will further enhance the role of compression molding in the EV battery industry.
- Advanced Material Development: New materials with improved properties, such as higher thermal conductivity and greater strength, will be developed specifically for compression molding applications in EV batteries.
- Process Automation: Increased automation will improve the efficiency and productivity of compression molding, reducing manufacturing costs.
- Integration with other Technologies: Compression molding will be integrated with other manufacturing processes, such as 3D printing and injection molding, to create even more complex and innovative battery components.
Compression molding is a valuable manufacturing process for producing high-quality, reliable components for EV batteries. Its ability to handle advanced materials, create complex geometries, and maintain tight tolerances makes it an essential technology for meeting the demands of this growing industry.