Let’s be honest; we all know blow molding. It’s the process behind those ubiquitous plastic bottles we use every day. Your shampoo bottle, that soda you grabbed from the convenience store, even the milk jug in your fridge – they’re all products of blow molding.
But here’s the thing: this technology is way more versatile than you might think. It’s used to make everything from car parts and kayaks to those giant inflatable decorations you see during the holidays. So, let’s dive in and explore the amazing world of blow molding.
Multi-Layer Magic: Keeping Your Snacks Fresh and Your Fuel Safe
Ever stopped to think about how those juice boxes keep your drinks fresh for so long? Or how those squeezable yogurt pouches prevent messy spills? It’s all thanks to the magic of multi-layer blow molding. This technique uses different types of plastic to create a container that’s not only strong but also acts as a barrier to keep the good stuff in and the bad stuff out.
Imagine it like a delicious sandwich. You’ve got your outer layers of bread for strength and structure, and then you’ve got your fillings – maybe some cheese, some meat, some veggies. In multi-layer blow molding, those “fillings” are different types of plastic, each chosen for its unique properties. Some layers might be super strong, while others might be excellent at preventing oxygen or moisture from passing through.
This is a game-changer for food packaging. It helps extend the shelf life of products, prevents spoilage, and keeps things tasting their best. But multi-layer blow molding isn’t just for food. It’s also used for things like fuel tanks, chemical containers, and even medical supplies. Those extra layers provide an added level of safety, preventing leaks and ensuring that potentially hazardous materials are securely contained.
Blow Molding Gets Complex: From Car Parts to Kayaks (and Beyond!)
You might be surprised to learn that blow molding can create some incredibly complex shapes. We’re not just talking about simple bottles here. Think about the sleek curves of a car bumper, the intricate design of an air duct, or even the hollow hull of a kayak. All of these can be produced using blow molding.
So how does it work? Imagine taking a hollow tube of heated plastic (called a parison) and placing it inside a mold. Then, you blow air into the parison, causing it to expand and take the shape of the mold. It’s like blowing up a balloon inside a container – except with plastic and a lot more precision!
With advancements in technology, blow molding can now create parts with incredible detail and intricate designs. This opens up a world of possibilities for various industries, from automotive and aerospace to healthcare and consumer goods.
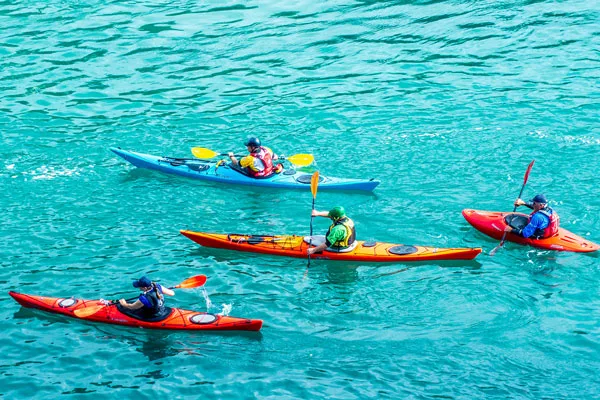
Kayaks
A Greener Way to Blow Mold: Recycling and Plant-Based Plastics
We all know that plastic waste is a major environmental concern. But the good news is that the blow molding industry is actively seeking sustainable solutions.
One of the most promising approaches is using recycled plastics. That empty water bottle you toss in the recycling bin? It could have a second life as a new container, thanks to blow molding. By incorporating recycled content, we can reduce our reliance on virgin materials and help keep plastic waste out of landfills.
Another exciting development is the use of bioplastics in blow molding. These plastics are made from renewable resources like plants, offering a more eco-friendly alternative to traditional petroleum-based plastics. This helps reduce our carbon footprint and lessen our impact on the environment.
Innovations in Blow Molding Technology
The field of blow molding has seen significant advances over the years thanks to innovations in machinery and materials. Smart manufacturing techniques, including the Internet of Things (IoT), are being integrated into blow molding operations. This allows for real-time monitoring and optimization, leading to increased efficiency, reduced waste, and higher quality output. Additionally, advancements in computer-aided design (CAD) have made it easier for engineers to create intricate molds that can reflect the complexity of modern designs.
Future Developments in Blow Molding
- Enhanced Sustainability: The push for eco-friendly solutions will drive more companies to invest in sustainable materials, recycling initiatives and biodegradable alternatives.
- Smart Manufacturing: As the Industry 4.0 concept takes hold, integrating IoT and automation into blow molding processes will become increasingly common, enhancing efficiency and reducing manual errors.
- Advanced Materials: Innovations in materials science will lead to the development of new polymers tailored to specific applications, enhancing performance characteristics in different environments.
- Collaboration and Innovation: As industries grow more interconnected, collaboration between manufacturers, designers and consumers will foster innovation, leading to novel applications of blow molding technologies.
Blow molding is a remarkable technology that continues to evolve and adapt to the ever-changing landscape of manufacturing and consumer needs. Its versatility and potential to create everything from everyday products to high-performance components across a wide range of industries is truly impressive. With sustainability becoming increasingly critical, the blow molding industry is poised to lead the way in responsible plastic use and innovative design. Whether for packaging, automotive parts, or complex consumer goods, the impact of blow molding will undoubtedly be felt for many years to come, making it a technology that is more than just about bottles; It’s about shaping the future.