Liquid silicone rubber (LSR) molding is like the tiny dancer of the manufacturing world – graceful, precise, and capable of incredible feats in a small package. This process is all about miniaturization and high precision, pushing the boundaries of what’s possible with silicone. From intricate medical components to complex multi-material designs, LSR molding is meeting the demands of today’s cutting-edge technologies.
What is LSR Molding?
LSR molding involves injecting liquid silicone rubber into a mold to create precise and detailed parts. The process starts with the creation of a silicone rubber compound, which is then mixed with other additives to achieve specific properties such as flexibility, hardness or color. This mixture is then injected into a mold, where it solidifies and takes the shape of the desired part.
Micro-Molding with LSR: Creating Medical Marvels
Imagine medical devices so tiny they can navigate the human body with ease, delivering life-saving treatments or performing delicate surgeries with minimal invasiveness. That’s the power of micro-molding with LSR.
This technique allows us to create incredibly small and intricate components with astonishing accuracy. We’re talking about parts that are often smaller than a grain of rice, featuring tiny channels, valves, and other features that were once impossible to manufacture.
LSR is the perfect material for this task because it’s biocompatible, chemically inert, and incredibly stable. It can withstand sterilization processes, resist degradation from bodily fluids, and remain flexible even in the tiniest of components.
Micro-molded LSR components are used in a wide range of medical applications, including:
- Catheters and Stents: Delivering medications or opening blocked arteries with greater precision and less discomfort for patients.
- Implantable Sensors: Monitoring vital signs or delivering targeted therapies from within the body.
- Microfluidic Devices: Performing lab tests on a tiny scale, enabling faster diagnostics and personalized medicine.
- Drug Delivery Systems: Providing controlled release of medications over time, improving treatment efficacy and patient compliance.
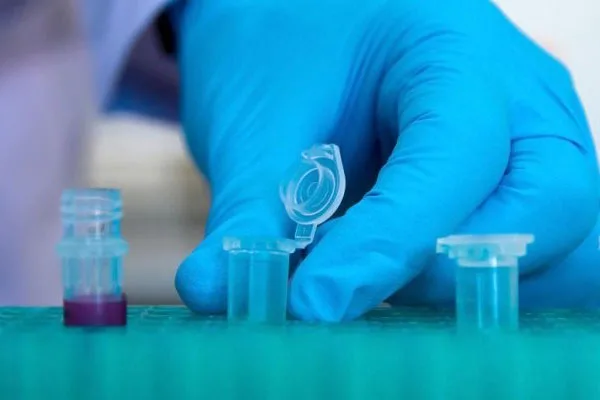
Silicone medical small bottles
Two-Shot LSR Molding: Complexity in Two Parts (or More!)
Sometimes, a single material just isn’t enough. That’s where two-shot LSR molding comes in. This technique allows us to combine different types of LSR or even combine LSR with other materials like thermoplastics.
Think of it like a culinary masterpiece with multiple layers of flavor and texture. Two-shot LSR molding allows us to create complex parts with varying properties, such as:
- Soft-touch surfaces combined with rigid structural elements.
- Components with integrated seals or gaskets.
- Devices with different colors or textures for improved usability or aesthetics.
This process opens up a world of possibilities for designers and engineers, enabling the creation of innovative products with enhanced functionality and performance.
Automation and Process Control: Ensuring Precision and Repeatability
When you’re dealing with tiny parts and intricate designs, precision and repeatability are paramount. That’s why automation and process control are essential in LSR molding.
Automated systems can precisely control the injection of LSR into the mold, ensuring consistent shot size and material flow. This minimizes variations in part dimensions and properties, leading to higher quality and reduced waste.
Sophisticated sensors and control systems monitor key process parameters like temperature, pressure, and cure time. This real-time feedback allows for adjustments to maintain optimal conditions and ensure consistent part quality.
By embracing automation and process control, LSR molding can meet the stringent requirements of industries like healthcare, automotive, and electronics, where precision and reliability are non-negotiable.
LSR molding is a game-changer in the world of miniaturization and high precision. With its ability to create intricate medical components, complex multi-material designs, and highly accurate parts, LSR molding is shaping the future of technology.