When it comes to creating crystal-clear lenses and light guides for applications demanding exceptional optical performance, Liquid Silicone Rubber (LSR) molding has emerged as a leading technology. In this state-of-the-art fabrication process, the highest levels of precision, clarity, and hardness are achieved, making this process well-suited to nearly every optical element.
Unveiling the Optical Advantages of LSR
LSR possesses inherent characteristics that make it particularly well-suited for optical applications. Its exceptional transparency allows for high light transmission, reaching up to 90% in some grades. Thus, LSR lenses and light guides transport light with very low loss, optimizing the performance of lighting systems, displays, and other optical devices.
Additionally, LSR is extremely stable when subjected to environmental effects that severely degrade other materials’ performance. Its ability to resist yellowing and degradation under prolonged ultraviolet and extreme heat exposure guarantees the transparency and reliability of optical modules over time.
The Precision of LSR Molding
The manufacturing process bears a vital role in achieving just the right optical properties required by lenses and light guides. LSR molding is performed on specially designed machinery, which permits the strict control of temperature, pressure, and other vital parameters in narrow bands. This ensures consistent and accurate production of optical components with exceptional surface finish and minimal internal stress, which can affect light transmission and clarity.
Some critical process parameters that are responsible for the accuracy of LSR molding towards optical application are:
- Mold Temperature Control: Maintaining exact mold temperatures (±1°C) is very important to maintain uniform curing and prevent defective pieces with irreversible adverse optical effects.
- Automated Material Mixing: Automatic mixing units guarantee that the two-component LSR material is properly mixed, assuring no changes in material properties and optical clarity.
- Clean Room Conditions: Manufacturing in clean room facilities reduces the possibility of contamination by dust and other particles that may degrade optical surfaces.
- Real-time Pressure Monitoring: Continuous monitoring of injection pressure allows for precise control of the molding process, ensuring consistent mold filling and preventing defects.
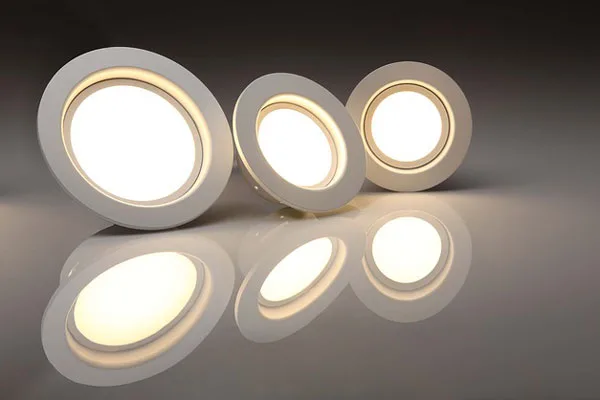
LED lights
Illuminating Applications in Modern Technology
LSR optical components are found in a growing number of applications, including:
- LED Lighting: LSR lenses are used in LED lighting systems to efficiently direct and focus light, enhancing energy efficiency and lighting quality.
- Automotive Displays: LSR light guides are critical in automotive displays, ensuring uniform backlighting and enhancing visibility.
- Medical Devices: Liquid silicone rubber (LSR) is ideal for medical products (e.g. endoscopes, surgical lighting) due to its biocompatibility and transparency.
The demand for LSR in optical applications is steadily increasing, driven by the growth of these industries and the ongoing development of new and innovative optical technologies. According to market data, the optical applications for LSR are growing at a rate of 15% per year. The increasing use of LED lighting drives this growth, advances in automotive display technology, and the growth of medical imaging devices.
Ensuring Quality and Performance
To guarantee the optical performance and reliability of LSR components, rigorous quality control and testing procedures are essential. Every batch of LSR is tested on:
- Optical Transmission Testing measures how much light passes through the LSR material;. This allows us to determine whether the light transmittance is up to specs.
- Dimensional Accuracy Checks: Taking precise dimensional readings to ensure the parts fall within tolerances so as to fit and work.
- Surface Quality Inspection: The surface of the LSR components is inspected for any defects or imperfections that could affect optical performance.
- Stress Pattern Analysis: This approach is employed to determine any interior stresses in the LSR material that may cause distortion or cracking over time.
Partnering with LSR Molding Experts
Collaborating with experienced LSR molding vendors is critical to the achievement of your optical component. The right partner will have the technical knowledge and practical experience to guide you through the entire process, from material selection and design optimization to manufacturing and quality control. They can help you choose the right LSR grade, design features, and molding parameters to achieve the desired optical performance.
LSR Molding: A Clear Choice for Optical Excellence
Hence, SR molding represents an attractive compromise in optical applications. Outstanding clarity, stability, and accuracy make it perfect for high-performance lenses, light guides, and other optical applications. Pair up with knowledgeable LSR molding professionals to utilize this technology for your optical requirements.
If you’re ready to explore the possibilities of LSR molding for your optical project, contact Nice Rapid’s technical team today. We would love to hear about your unique requirements and help you find the appropriate ways to meet your optical needs.