When you think of pressure die casting, the first industry that comes to mind is the automotive industry. After all, this manufacturing process is famous for creating high-precision components found in everything from engine blocks to transmission housings.
But pressure die casting’s applications don’t stop there. Other industries—consumer electronics, aerospace, and even medical devices—are using the process to produce complex, durable, yet lightweight parts. Let’s look at some of the surprising ways in which pressure die casting is changing many industries.
What Is Pressure Die Casting?
Pressure die casting is a process of manufacturing in which molten metal is forced into a steel mold under high pressure. The result is a precise, repeatable process with excellent dimensional accuracy and surface finish. The common materials are aluminum, magnesium, and zinc alloys. Thus, it is perfect for applications requiring lightweight with high strength.
While automotive manufacturing has traditionally been the largest consumer of die-cast components, advancements in the process have opened doors to a host of other industries.
Pressure Die Casting in Consumer Electronics
The consumer electronics industry has seen a surge in the use of pressure die casting for creating sleek, high-performance devices.
Smartphones and Laptops
- Lightweight Frames: Aluminum die-cast frames provide durability and a premium feel to devices like smartphones and laptops.
- Heat Dissipation: Die-cast components are often used in heat sinks and other parts critical for managing the thermal performance of electronic devices.
Audio Equipment
- Speaker Housings: The precision of pressure die casting ensures airtight seals and superior acoustic performance in high-end speakers and headphones.
Die casting enables the production of intricate designs and reduces weight without compromising strength, helping electronics manufacturers meet consumer demands for slimmer, more powerful devices.
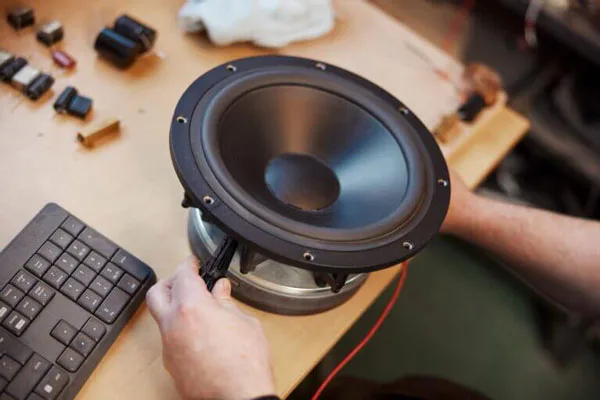
Speaker housings
Aerospace Industry Applications
Pressure die casting has become an essential manufacturing method in the aerospace sector, where performance and weight are critical.
Aircraft Components
- Engine Parts: Lightweight magnesium and aluminum die-cast components are used in jet engines and auxiliary systems.
- Structural Components: From brackets to housings, die-cast parts are valued for their strength-to-weight ratio and reliability.
Space Exploration
Die-cast parts are not limited to aircraft—they’re also finding applications in spacecraft. The precision and lightweight properties of die-cast alloys make them ideal for use in satellites and exploration vehicles, where every gram counts.
Medical Device Manufacturing
The medical device industry is another area where pressure die casting shines, thanks to its ability to create highly detailed and precise components.
Surgical Instruments and Equipment
- Handheld Devices: Compact and durable casings for surgical instruments are often made using die-cast magnesium or aluminum.
- Imaging Equipment: Die casting is an excellent choice for parts for X-ray and MRI machines, as they require tight tolerances and lightweight materials.
The biocompatibility and corrosion resistance of certain die-cast alloys further enhances their suitability for medical applications.
Renewable Energy Systems
As the world moves toward greener energy solutions, pressure die casting supports renewable energy systems.
Wind Turbines
Die-cast components like housings and brackets are assembled into wind turbines. These parts must withstand the most extreme environmental conditions, so die casting’s strength and precision are imperative.
Solar Power
In solar panel installations, die-cast aluminum parts are used for mounting systems and structural supports. These components combine lightweight properties with durability, ensuring long-term performance.
Advantages of Pressure Die Casting Across Industries
The widespread adoption of pressure die casting in these industries is driven by several key advantages:
- Cost Efficiency: High production rates and minimal material waste make die casting a cost-effective option for large-scale manufacturing.
- Design Flexibility: The ability to create complex shapes and thin-walled components enables innovative product designs.
- Material Versatility: A wide range of alloys ensures that the process can be tailored to meet specific performance requirements.
Why Choose Nice Rapid for Pressure Die Casting?
At Nice Rapid, we cater to the need for high-quality pressure die-casting solutions for different industries. Equipped with state-of-the-art technology and a quality commitment, our company helps others create components that meet exacting standards for precision, durability, and performance.
Whether in consumer electronics, aerospace, or renewable energy, Nice Rapid’s expertise and innovative spirit help bring your ideas to life. Our global footprint and commitment to sustainability make us the perfect partner in helping companies utilize the full potential of pressure die casting.
Conclusion
The versatility of pressure die casting goes beyond the automotive industry. From consumer electronics to aerospace, medical devices, and renewable energies, this manufacturing process is changing how we make strong, lightweight, and complex components. With every new day, as the technology continues to advance, so too will the potential applications of die casting, creating exciting possibilities for industries throughout the world.
If you’re ready to explore pressure die casting’s benefits for your business, contact Nice Rapid today. Let us help you innovate and achieve excellence in manufacturing