How to Prevent Injection Molding Flash?
Flash is a common defect in injection molding, describing the thin layer protruding from the mold parting line or areas around the mold where two contradictory surfaces meet, forming a physical boundary.
Such areas create differences in material expansion during production and other factors contributing to flash. Flash most commonly affects the parting line, but other high-risk areas exist for this occurrence.
The causes and effects of flash remain similar, regardless of the location of the mold. Most modern manufacturers don’t eliminate flash but try to perfect the manufacturing process to produce as little as possible.
There’s always the option to purchase flash-free molds. However, they come with high price tags. Manufacturers must balance factors like cost, waste, aesthetics, and quality when selecting their tooling.
Is there any other way manufacturers can reduce flash in production processes? Let’s look at the reasons behind the cause of the flash and discuss solutions to the problem.
The Main Causes of Injection Molding Flash
Mismatches of the Parting Line
As mentioned, flash is most common along the parting line. In most instances of this problem, debris causes misalignment of the mold halves, which operators don’t pick up. Excess material leaks out of the opening, causing a flash.
Mold design flaws are also responsible for this issue. Typically, the mold’s flaws exacerbate and worsen over time rather than stabilize.
Old tooling may result in a flash due to material leaks. Wear and tear of the mold results in mismatches and the occurrence of flash.
Flash can still occur when you have new tooling and no contaminants. Improper mold clamp pressure or extremely complex mold cavity designs can result in mismatching of the parting line.
Single-shot over-molding applications require using a single-barrel injection molding machine and preformed substrate to add additional layers of material to the final product.
Improper Venting
The intricate processes involved in injection molding require the operator to monitor the overall pressure, temperature, air pockets, and other factors during the molding process.
For example, air bubbles trapped in the material and mold create product flaws, affecting the components’ overall load-bearing and mechanical properties.
Nozzle & Barrel Temperature
Pressure isn’t the single factor increasing material viscosity, resulting in flash in injection molded components.
The nozzle and barrel temperature directly affect the process as well. Higher temperatures make the material prone to leaking due to low viscosity, resulting in increasing chances of creating mold flash.
Low Material Viscosity
A liquid’s viscosity refers to its flow. Correct material viscosity is central to a successful injection molding process.
Lower viscosity materials provide easy flow in the mold shape and create distortions resulting in a flash. Typically, viscosity results from a combination of factors, including material properties, temperature, speed, and pressure.
Over-Pressurized Mold
Pressure is a key component in molding, and managing it is imperative to successful molding and flash reduction.
Increased pressure results in increased temperature and flow in sealed environments. The increased molding pressure and elevated viscosity can create several defects, including flash.
Over Filled Mold
Overfilling the mold tests the limits of its geometrical and size restrictions. Injection pressures in overfilled molds typically overcome clamping forces, resulting in leakages and the formation of flash and other production defects.
Operators should be careful when adjusting feed rate settings. The cooling of material contracts plastic materials, resulting in incomplete components due to “short shots” in the injection molding process.
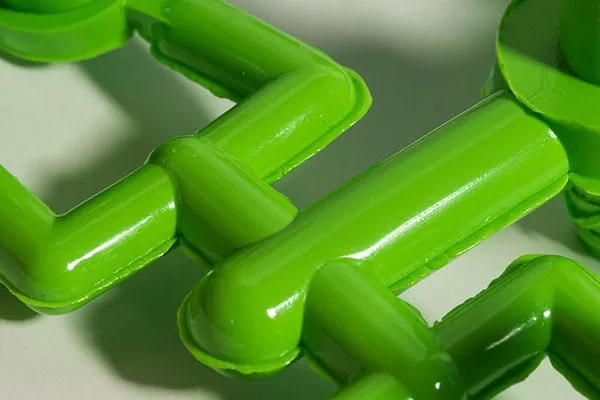
How to Prevent Injection Molding Flash?
Design for Function
Manufacturers should design molds for function and simplicity rather than complexity. For instance, if we consider the mold parting line, experts recommend using an edge-style parting line rather than a surface.
This strategy has functional and aesthetic benefits as it makes the parting line invisible. This method reduces the chances of creating flash as seams will counter-parting line mismatches.
DFM Analysis
DFM(Design for Manufacturing) analysis is a critical component of any injection molding project. Special software programs simulate the manufacturing results, displaying the material flow characteristics and predicting issues like flash, warping, and flux during injection molding processes.
This strategy has functional and aesthetic benefits as it makes the parting line invisible. This method reduces the chances of creating flash as seams will counter-parting line mismatches.
Slower Injection Rates
Reducing friction in the molding process reduces flash, and one of the best ways to eliminate friction is to control process variables.
Injection rates affect pressure, temperature, and viscosity, creating flash. Typically, manufacturers use this first strategy to deal with flash since most process variables are linked to injection rate.
Over-molding is usually performed by a multi-barrel injection molding machine, with the process of adding material to the component shortly after forming the substrate to create strong material bonds.
Flash-Free Molds
Using a flash-free mold is an effective but pricy method for eliminating flash from molded parts. You get guaranteed flash-free results, but the tooling cost is excessive and might not be viable for budgets or applications.
When functionality, accuracy, and aesthetics are a top priority, it may justify the purchase of this tooling for defect-free parts.
Proper Maintenance and Mold Cleaning
One of the most frequently cited reasons for mismatches on the mold parting line is an accumulation of debris, dirt, and surface contaminants. Microparticles trapped in mold cavities can cause material overpacking, increasing the chances of defects in manufactured parts.
Keeping the mold as clean as possible between production runs helps to remove surface contaminants and reduce defects. Similarly, proper mold maintenance mitigates the risk of defects like a flash and ensures optimal results in product formation and curing.
Improve Processes
Improving molding processes and optimizing them to reduce flash and other molding defects assist manufacturers with creating repeatable results. The manufacturer should have SOPs in place to overcome all challenges in the molding process to reduce flash and defects.
Ensuring the correct clamp pressure and tonnage prevents issues with damaging the mold surfaces and creating deformations in the mold that result in multiple product defects.
In Closing – Find the Right Injection Molding Partner
Unfortunately, some degree of mold flash will always be present in injection molding processes. Unless you’re using flash-free molds, it’s hard to avoid it. The best strategy for reducing mold flash is through optimizing production processes and monitoring for errors and areas for improvement.
Manufacturers should improve design instead of focusing on common causes of flash in molded components. Implement a regular maintenance schedule to ensure mold surfaces are contaminant-free. Through consistent process improvement, reducing flash and material waste to a minimum in production is possible.