Recent articles in the engineering press have been looking to the future of 3D printing and how it can be used to make production easier and faster, whilst at the same time keeping the quality that we have taken for granted with injection molding and other similar production techniques.
Aviation has been a large growth area in advances in both standard manufacturing and 3D printing, which is a significant breakthrough for any technology that must meet very strict requirements, such as that necessary for passenger-carrying aircraft. Even more interestingly, Space seems to be not necessarily the final, but the current frontier for 3D printing with many applications being studied that investigate how 3D printed materials and parts cope with use in a vacuum and how they would perform if fitted to, for example, the International Space Station for an extended period of time.
It has been no secret in the aviation world that Airbus have been interested in 3D printing for a long time and this does not necessarily just mean the printing of small, non-critical parts. Airbus would like to print as much of a plane as possible and, to this end, are bringing together many of their suppliers and manufacturers together, in order to decide exactly what is able to be 3D printed and what is not. It is clear that if they succeed in this, they will reduce a lot of the cost of transporting parts around the world, as well as reducing stocks of parts and the number of storage facilities required.
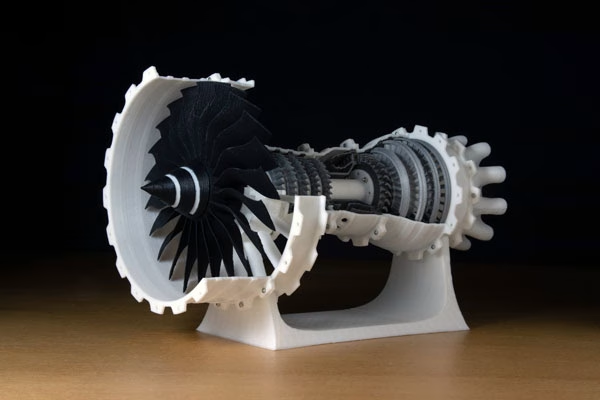
3D printing airlines
3D printing parts will also benefit airlines, as they will be able to print replacement parts for fitting pretty much instantaneously, reducing downtime and passenger compensation bills, which can be hefty – especially if passengers need to be rerouted on other carriers or accommodated in hotels overnight whilst waiting for a part to arrive. Such a strategy will also suit operators of older Airbus models, as parts that are no longer in official production can be officially sanctioned and created by Airbus and fitted to older variants, thus ensuring Airbus quality and safety throughout the lifespan of the airframe.
Recently, the first titanium 3D printed bracket has already been fitted to a commercial Airbus model – the A350 XWB – showing the dedication and desire that Airbus has to make the remote printing principle work in practice. Even more intriguingly, this 3D printed part will be produced and fitted as part of the standard production process and has already received certification by the main aviation regulatory bodies. The same has also already been undertaken in the field of aircraft jet engine production, with General Electric using 3D printed fuel nozzles throughout the LEAP range of engines.
Another huge benefit of producing parts using 3D printing techniques is that they are generally more cost effective to produce than traditional injection molding methods. Primarily, this is due to 100% computer controlled production processes taking less time to produce the part and the reduction of initial material necessary to create the same part. For example, the titanium bracket used in the A350 XWB is produced with virtually no material wastage, due to its sophisticated laser printing method. Such a production method is used to both produce the part to its exacting specifications in the initial production stages, as well as to check the finished part for manufacturing tolerances when it has been completed – both extremely important in the aviation environment.
It is very interesting to see from this small snapshot of 3D production in aviation how 3D printing has advanced since the early days and we can only but wonder what the future has in store!
At NICE Rapid we specialise in all types of rapid tooling and injection molding – please contact us when deciding on your next project, as we would love to hear from you.