3D printing has experienced huge advancements in this revolutionary technology in the three decades since its inception. It continues to disrupt the way companies approach their product development initiatives.
Materials science and instrumentation improvements in 3D printers deliver enhanced throughput and performance, cost and production efficiency, and scalable operation. From prototyping to production, every aspect of 3D printing makes progress in leaps and bounds with each passing year.
Stereolithography 3D printing is an example of these tech advancements, allowing medical device OEMs to leverage the ever-expanding range of printing materials to produce precision parts with high accuracy, slick topography, and affordable production scaling.
1 Medical Device Prototyping
Fast-tracking the prototyping of new medical devices is essential for bringing new products to market that create improvements in patient care in the healthcare industry. Until recently, product prototyping and testing could take years to get a new medical device to market.
The advancements in 3D printing dramatically slashed prototyping timeframes, allowing OEMs to complete their projects in weeks or days.
The limitless forms available through 3D printing make it ideal for medical device prototyping, with no specialist tooling requirements.
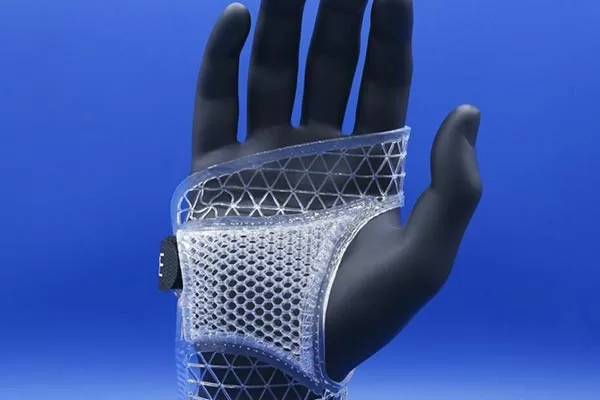
Custom medical devices wrist guard
2 Biocompatible and Sterilizable Materials
Medical devices require sterilizable and biocompatible parts, with SLA offering a comprehensive range of materials for medical applications.
With more than 30+ materials available for SLA 3D printing prototype design, device prototyping can meet the rigorous demands of medical and ISO standards.
BioMed Clear is an example of a biocompatible, medically-certified resin offering durability and strength for long-term mucosal or skin contact.
It’s the ideal material for device components requiring minimal water absorption properties and resistance to wear and tear. BioMed Clear 3D printed components include items like implants and surgical tools.
1500 resin offers manufacturers a resilient material with similar performance and strength characteristics as traditional plastics like Polypropylene (PP).
This sterilizable material is certified for use in device components requiring permanent contact with the skin. As a result, it’s the ideal material for use in personal protective equipment (PPE) and wearables.
Elastic 50A offers a pliable and soft material suitable for prototyping medical device components that would otherwise require manufacture in silicone. However, with Elastic 50A, you do away with the need for investment in expensive tooling. This material is ideal for prototyping grips, handles, gaskets, and masks.
3 High-Quality, Precise, Accurate Surfaces
SLA 3D Printing technology offers a high level of accuracy in component manufacturing, with tolerances as low as -0.025mm (25 microns).
That’s less than the width of a strand of hair, giving device and component manufacturers higher accuracy and precision than conventional production techniques and manufacturing processes.
A key benefit of 3D printing is the high-quality finish left on component surfaces, similar to what manufacturers achieve with plastic and silicone injection molding techniques.
4 Reductions in Production & Manufacturing Costs
3D printing offers OEMs better economies of scale in their manufacturing processes, lowering costs. The ability to print multiple parts and eliminate the need for tooling make 3D printing ideal for mass manufacturing medical device components and low-volume production applications.
In conventional manufacturing methods, production expenses scale linearly with the number of components produced. However, 3D printing uses a digital model to make as many parts as required.
The simultaneous manufacturing of components is achievable at several sites in different locations. There’s no tooling requirement, as 3D CAD models are all that’s required to ensure conformity in all component specifications.
This feature of 3D printing and manufacturing processes allows OEMs to manufacture components on demand in local markets. Manufacturers save on input costs relating to logistics and transport, environmental impact, and timescales by delivering components and devices directly to end-consumers.