Compression molding is a process that has been around for hundreds of years. It makes metal castings, plastic injection molded parts, and composite parts. This post will explore some surprising benefits of compression molding that you might need to learn about.
High Strength
Compression molding is a popular manufacturing process due to its ability to create high-strength components. In addition, compressing heated materials into a mold allows for greater control of the component’s shape and thickness and reduces the amount of waste produced.
The high-pressure molding process creates a durable component with a consistent finish and surface quality. It makes compression molding an ideal choice for applications that require strong components with reliable performance.
Low Cost
Another benefit of compression molding is its low cost. Compression molding is relatively easy to set up compared to other manufacturing processes and does not require a large investment. As a result, it makes it a popular choice for businesses that want to produce small quantities of high-quality parts without breaking the bank.
Rapid Manufacturing
Compression molding is also highly efficient in terms of manufacturing speed. The process can create parts at rates of up to one hundred pieces per minute, which makes it an ideal choice for applications that require fast turnaround times.
In addition, since the components are precision molded, there is little room for error and no need for extra tooling or fixtures. It makes compression molding ideal for quickly producing prototype parts or production-ready products.
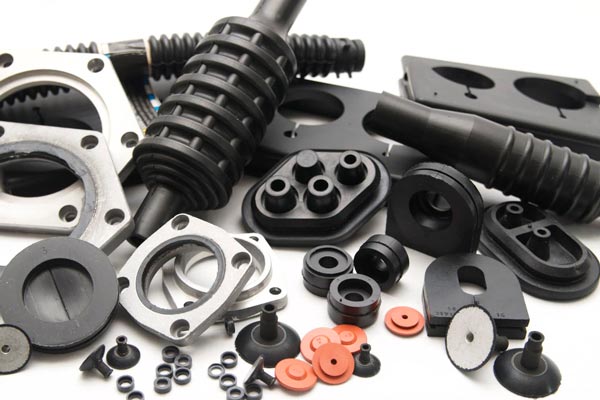
Rubber molding products
Minimal Waste
One of the key benefits of using compression molding is its ability to reduce waste production. Compressing the heated materials into mold limits the amount of waste produced. As a result, businesses can save on material costs and disposal fees.
Furthermore, since the components are precision molded, there is little need for additional finishing or assembly work. It minimizes the amount of time and effort that is needed to produce finished products.
Flexible Design Space
Compression molding is a popular plastic manufacturing process that offers many benefits. One of the greatest advantages of this process is its flexibility when it comes to design space.
Compression molding allows designers to create intricate shapes and parts with complex geometries that would be impossible with other manufacturing processes.
Additionally, the molding process is more cost-effective than other methods, allowing designers to experiment with design ideas without incurring large expenses. Finally, the flexibility of compression molding makes it an ideal choice for various applications.
Durability
One of the key benefits of using compression molding is its ability to create exceptionally durable components. In addition, compressing heated materials into a mold allows for greater control of the component’s shape and thickness and reduces the amount of waste produced.
Additionally, the high-pressure molding process creates an exceptionally durable component with a consistent finish and surface quality. This makes compression molding an ideal choice for applications that require strong components with reliable performance.
Reduced Weight
Compression molding is becoming increasingly popular for its ability to produce lightweight parts and components. This process involves placing a pre-measured material in a mold cavity and then applying pressure to shape the material into the desired form.
This method allows manufacturers to produce parts with thinner walls and complex shapes while maintaining structural integrity. As a result, compression molding can greatly reduce the overall weight of a product while still providing strength and durability. It can help to improve fuel efficiency and reduce the environmental impact of transportation.
Heat Resistance
Heat resistance is an important benefit of compression molding, as it allows for producing parts that can withstand higher temperatures without sacrificing structural integrity.
Compression molding offers a wide range of temperature resistance, producing parts suitable for various applications.
Compression molding can produce parts that can withstand temperatures up to three hundred degrees Celsius by using high-temperature-resistant materials and controlling the part geometry. As a result, it makes it an ideal choice for components exposed to extreme temperatures.
Appearance
Compression molding offers many benefits, such as creating intricate designs and shapes, making it ideal for consumer electronics and automotive parts applications. The compression moulding molds also allow for a better surface finish, enabling smoother surfaces with fewer flaws and imperfections. These qualities make compression molding an ideal choice for parts that need a high-quality appearance.
Conclusion
These are just some of the surprising benefits that compression molding offers to end users. If you are looking for a process that will produce high-quality, durable, and cost-effective products, consider compression molding as an option for your manufacturing needs.