Today, manufacturers and prototype designers have their choice of finishes in plastic injection molded parts. The possibilities for finishes of final products allow better levels of innovation and creativity to come bubbling to the surface in the design process.
The tooling is critical in the plastic injection molding process, allowing for different product surface textures. There are five common methods of creating mold finishes for different product textures.
Air Blasting
Pressurized air sprays a variety of abrasive materials against the tool’s surface. Aluminum oxide, sand, and nut shells are common examples of the spray medium. Each medium creates a different finish according to its abrasive properties and the air pressure involved in the process. Blasting is inexpensive and quick, creating a flat, matte finish on the tool.
Polishing & Sanding
Tool machining leaves behind marks on the mold that transfer to the product unless removed before manufacturing. Polishing and sanding mold tools remove surface problems using diamond burrs, rotary tools, files, sandpaper, and other common abrasives.
Textures produced can range from coarse grain or mirror finish. Hand polishing typically leaves a global effect, not an obvious cosmetic design or effect. Sanding takes skill, but technicians can’t access thin sections or deep pockets.
EDM Spark Erosion & Tool Finishing
Electrical Discharge Machining (EDM) uses a copper or graphite electrode in a water or oil electrolytic bath to spark the tool wall. The mold material melts but is immediately cooled by the bath, creating thermal shock, and fragmenting the metal into particles that flush away.
The process is almost instantaneous and ideal for use on soft or hard metals. Manufacturers use this method for tight tolerances and finishing hard-to-reach areas like thin, deep slots, sharp concaves, debossed letters, and other complex features.
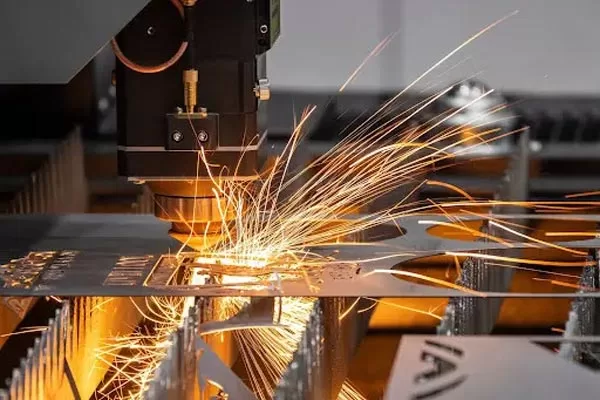
Laser cutting
Laser Etching
Laser etching allows the mapping of any texture onto curved surfaces. This process involves the use of 3D computer modeling. This technology lets the designer align the contours of moldable shapes with the texture map.
5-axis motion control uses laser tracking over the tool surface while reaching out-of-sight areas and undercuts.
The automotive industry requires laser-etched molds for dashboard manufacturing, where they need to maintain consistency over a length. It’s a more expensive method but produces ideal results, especially in CAD models.
Chemical Photoetching
Many plastic molded parts feature complex in-molded textures and patterns. Some finishes can emulate organic textures like leather, stone, and wood, while others offer an abstract geometrical design. Photoetching processes coat the tool wall with a light-sensitive material called a “photoresist.”
A UV light projects the required pattern onto the tool mold, curing the areas the light touches. The operator washes away the remaining compound, and a film mask remains. The mold goes to an acid batch where the acid etches away the unconditioned area, resulting in the required texture.
The operator must carefully control this process to ensure the metal type, design complexity, and acid penetration level of the material.
Etching is cost-effective and fast and produces fine textures suitable for any look in the final product. However, this technology does have some drawbacks. Etching isn’t ideal for areas that are out-of-sight or in undercuts. Some patterns may get geometrically distorted over lengthy curved surfaces.
Wrapping Up
Mold manufacturers can create tooling that’s ideal for any plastic application. Whether you need a rough or smooth finish, it’s possible to make the right tool for the prototyping project.
EDM and laser etching are the best choices for precise, complex finishes, while chemical photoetching and sandblasting are more general and affordable for projects. Choose the finish that aligns with your prototyping goals.