There is a domination of plastic injection products all around us. From toys to turbine blades in space shuttles, they are all made from plastic injection molding. For those who are unfamiliar with the process and want to understand its popularity, then this article will answer all your questions about plastic injection molding.
What is plastic injection molding?
Plastic injection molding is a cost-effective and efficient process for mass manufacturing plastic parts. The process requires the creation of a mold and involves injecting molten material into the mold and then letting it cool into a formed part.
The history of plastic injection molding can be traced back to 1872 when an American Inventor John Wesley Hyatt applied for the patent for the first injection molding machine. He has done this because he wanted to replace the ivory balls used in bowling with plastic. His product was unsuccessful, but his machine is another story.
It was Wyatt’s plastic injection molding machine that propelled the plastic injection molded products to its success. The industry has evolved from producing simple and basic parts like buttons, in the beginning, to difficult-to-produce medical equipment like we have today.
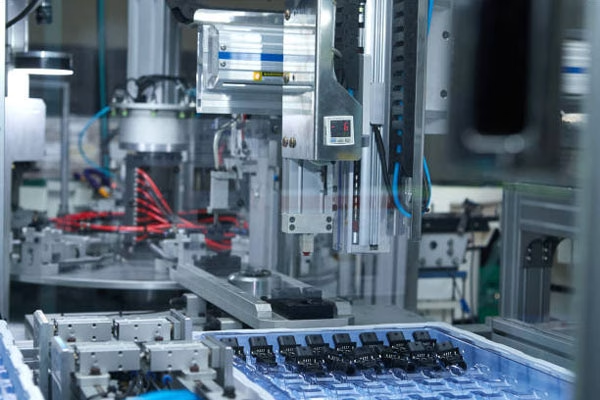
Injection molding machines
Products from Plastic Injection Molding
Manufacturers from all over the globe use plastic injection molding to create products in high volume. It can create anything from large objects like garbage bins to smaller objects like buttons and casings. Many people don’t know this, but the most common application of plastic injection molding is in non-consumer parts that do not require aesthetic appeal like mechanical parts.
How Does Plastic Injection Molding Work?
Plastic injection molding can be explained in four simple steps: a. melting the material, b. injecting this material into the mold, c. letting the material cure, and d. removing the material from the mold.
However, to understand the whole process we need to understand how the injection molding machine works. The process begins with feeding the plastic pellets from the hopper to the barrel. This barrel contains a plastic auger, which is a screw-shaped device that feeds the material by rotating. The heater bands on the outside of the barrel turn the place into a molten state.
The machine is closed once the machine is initiated, and the auger plunges forward due to the high pressure. It works like a syringe injecting the molten plastic into the empty cavity of the mold. A coolant, which is usually water, will act as a coolant as it continuously flows in and out of the mold through the channels. This helps cool down the molten plastic in less than 60 seconds.
When the plastic part solidifies, the mold will open and eject it. That completes the cycle. And once the product is ejected it will signal the process to begin again.
Final Note
Many manufacturing companies are offering plastic injection molding services because of the demand for the products. They provide a complete range from mold making to production capabilities. Companies can also avail of consultation and product distribution and benefit from a whole list of other in-house production services.