Compression molding uses a thermosetting process to shape materials such as rubber, composites, or resins. It’s a versatile manufacturing technique useful in rapid prototyping and low-volume manufacturing projects. This post examines the technology, its benefits, and its limitations.
Understanding the Compression Molding Process – A Brief Overview
Many industries rely on compression molding technology for product development and manufacturing. The process involves heating tooling to compress raw materials under pressure to create a specific shape.
Compression-molded components are economical to produce and highly durable, making them suitable for many applications. The manufacturer measures a specific amount of preheated molding material called the “charge” before inserting it into the heated mold to form the final product.
The molds feature a vertical pressing mechanism and preheated cavity to shape the desired product. As the charge expands in the mold, the excess material, known as “flash,” is trimmed by the manufacturer before shipping it to the client.
Compression molding is a seven-stage process, which we’ll outline below.
Step #1 – Mold Tooling Production
The manufacturer designs and builds the mold tooling using systems like 3D printing, die-casting machining, or a combination of the three.
Step #2 – Setting up the Molding Machine
The operator cleans the mold and preheats it to complete the setup process for molding the components.
Step #3 – Preparing the Charge
The operator selects the material for the project and determines the correct amount of material to minimize flash but ensure adequate compression and flow of material in the mold. Using too much material creates excess flash and waste, adding to project costs.
Step #4 – Inserting the Charge
The operator positions the charge in the preheated mold.
Step #5 – Compressing the Charge
They close the mold and apply pressure to the material under heat, allowing the material to flow into the mold contours and shape the final component.
Step #6 – Release
The operator releases the pressure on the mold and removes the finished component for final processing.
Step #7 – Trimming the Finished Components
The manufacturer trims the excess flash from the molded component, using a manual process, cleaning it up before any final assembly.
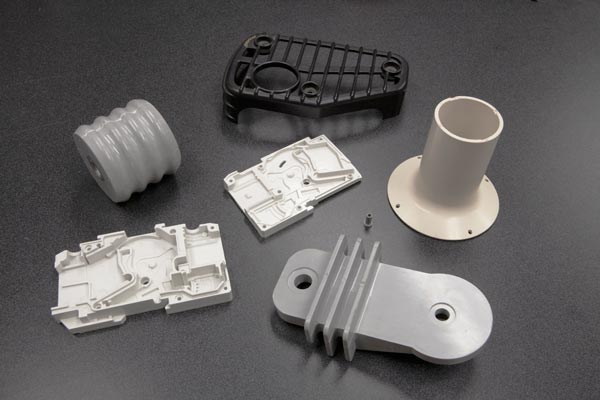
Silicone compression molding parts
The Types of Compression Molding Technology
Several compression molding techniques are used in rapid prototyping and low-volume manufacturing processes. Each method has unique properties and suits different applications, depending on the materials used and the project requirements for the finished component.
Benchtop Compression
This method is ideal for manufacturing small to medium-sized components. It’s a better choice for higher-capacity runs and requires less space than other methods.
The mold offers several access points, providing flexibility for the operator to remove the parts and trim the flash. Its small footprint makes it the best choice for factories with limited floor space.
Hydraulic Industrial Compression
These large machines are suitable for higher-volume production projects in commercial settings. They implement a hydraulic lift system to reach high-pressure levels during the molding process, resulting in the easy manufacturing of large parts with uniform consistency.
Wet Compression
This method is suitable for combining resins, epoxies, and liquids with solid materials. Wet compression molding tools are common in car part manufacturing to produce durable, strong, low-cost components.
Cold Compression
This process involves cold compression with no heat. The operator preheats the charge before placing it in the mold. However, soft materials may not require preheating before insertion into the mold cavity. By introducing heat to the process, manufacturers can control the compression and curing of the material to shorten production times.
Common Materials Used in Compression Molding
Compression molding suits thermoplastics and plastics. When heated, thermoplastic materials become soft and pliable and harden during cooling. They display no changes in mechanical and chemical properties after hardening and are suitable for multiple heating and cooling cycles.
Thermoset materials display different characteristics. These materials cure into a final form and cannot undergo further heating, or they experience changes to mechanical and chemical properties. Curing is permanent, and the product remains in its final form.
In Closing – What are the Limitations to Compression Molding?
While there are several benefits to compression molding, the process has limitations.
Flashing & Burrs
Molded parts must undergo manual removal and trimming by operators after molding, which results in material waste and additional time in the manufacturing process.
Unsuitable for Complex Component Manufacturing
Compression molding can’t produce highly intricate components with advanced design details. Parts requiring deep undercuts and other intricate design features may experience malformation or aeration of materials, ruining the structural integrity of the final component or interfering with the correct flow of materials in the mold, resulting in defective parts.
Slow Cycle Times
Plastic injection molding is the better choice for high-volume manufacturing tasks. It offers rapid cooling and ejection from the mold. Compression-molded parts require manual removal and trimming, resulting in longer cycle times and more labor in the production process.