Liquid silicone rubber molding involves mixing two compounds and heat-curing them in a mold with a thermoset platinum catalyst process to create flexible products and parts. Silicone moldings are durable and resistant to high temperatures, featuring a low compression set.
These characteristics make them ideal for use in baby products. LSR elastomers offer exceptional design flexibility and optical clarity, maintaining stable properties across a wide temperature range from -58F to 482F.
How is LSR different from Injection Molding?
Liquid Silicone Rubber (LSR) molding is similar to plastic injection molding in the mechanics involved with forming parts inside the mold. However, it differs in how the material cures. With plastic injection molding, the thermoplastic resins melt before being injected into the mold and cured under pressure.
LSR molding utilizes a two-stage thermoset compound cooled before injection into heated molds cured. Unlike thermoplastics, LSR offers permanent curing and setting, meaning it can’t be re-melted after curing.
The process combines thermoset compounds in a 1:1 ratio, generating a reaction heat-accelerating the conversion of liquid silicone rubber into a solid state.
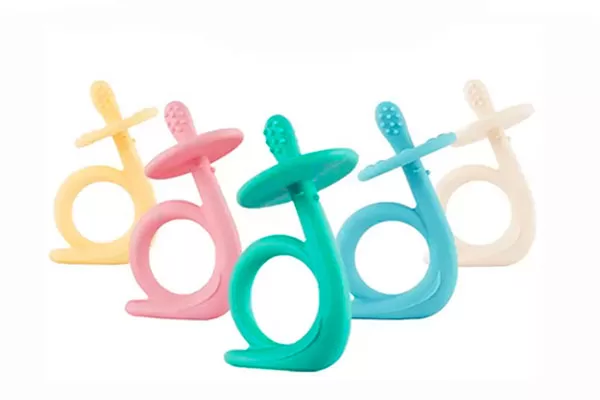
Silicone baby teething toys
Why Use Silicone Molding in Baby Product Design?
LSR molding is ideal for producing baby products due to the following characteristics of the moldings made.
Thin undercuts & Walls – With LSR molding, it’s possible to remove finished products with thin walls and undercuts from the mold without incurring damage to the parts or products. The excellent elongational and compression set properties maintain shape under stress.
Comfort & Softness – LSR products are smooth and soft to the touch. When combined with thermoplastics in two-shot or over-molded applications, LSR products offer rigid structural firmness and silky, soft texture.
Affordable production – LSR moldings are suitable for mass product production, allowing manufacturers to benefit from economies of scale in their processes.
Prevention of Air Traps – Baby products undergoing an over-molded two-shot process include sippy cup spouts and sealed caps to stop air infiltration. This feature is important to prevent the baby from swallowing air trapped in water and milk. Venting these products prevents this problem by adding valves, slits, or holes in specific locations on the bottle.
What are the Benefits of Using Liquid Silicone Rubber in Baby Products?
Hygiene – Food-grade LSR molding offers a clean automated production environment with minimal human interaction.
Hypoallergenic – LSR is hypoallergenic and removes the risk of skin irritation in infants.
Odorless and tasteless – LSR products such as sippy cups, pacifiers, and bottle teats don’t emit any chemical taste or smell. There’s no chance of the baby refusing the product due to adverse interactions with their senses.
Comfort & soft to the touch – LSR products have a smooth, soft texture and touch, making them ideal for breast-feeding and baby-feeding products.
Durability – The low compression set of LSR provides strength and durability against compression deformation. It’s also highly resistant to temperature changes, such as boiling a baby bottle during sterilization practices.
What Baby Products Feature Silicone Molding?
LSR moldings are a top choice for baby products. You’ll find LSR molding in the following products.
- Bottle nipples (teats).
- Sippy cup spouts.
- Teethers.
- Pacifiers.
- Bottle seals.
- Nipple protectors and breast pump accessories.