Manufacturing plastic parts would require additional finishing before its completion. The majority of this final processing is done to improve the product’s aesthetics and appearance. One of the most common finishes is the inclusion of mold surface textures.
What does this mean for injection molding? The surface finish of the product is critical to its appearance. Aside from aesthetics, the surface texture can also affect the performance of the product. Therefore, choosing the surface texture is crucial as it determines the look, feels, and performance of the product.
What is Surface Texture?
In the manufacturing industry, the surface texture refers to the three-dimensional topography of a product. Getting a flat surface topography or featureless surface is hard to find. Instead, you will find some kind of texture in most of them.
Some of the surface textures you’ll find are regularly repeating patterns, while some of them are random and difficult to categorize. Generally, texturing involves creating an array of patterns on the product’s surface.
In the US, many of the surface textures of injection molding products follow the standards set by the Society of the Plastics Industry or SPI. It defines the cosmetic quality of plastics into four categories.
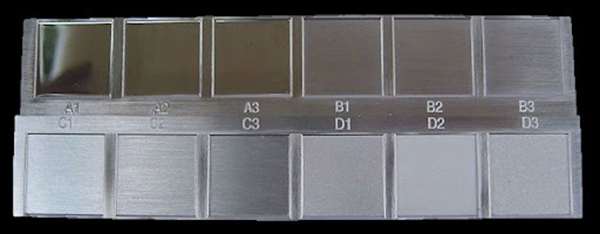
SPI surface finish
Shiny Finish
SPI grades A1, A2, and A3, stipulate a high gloss finish on the steel tool molds. It is buffed to a mirror luster using a fine diamond powder in oil. The resulting product exhibits a smooth, shiny, and expensive look, like in plastic visors, mirrors, and other optical products.
Semi-Gloss Finish
It falls into SPI grades B1, B2, and B3 where the hardened tool molds have a semi-gloss finish. It is achieved using ultra-fine sandpaper or emery cloth. The plastic products from these molds have no mold, tools, or machining marks.
Matte to Dull
This refers to SPI grades C1, C3, and C3, where the mold has a specific matte finish from polishing using fine stone powders. It does not show any tool, mold, or machining marks and is used in molding die-cast or thermoset industrial parts made from plastic.
Displaced Standard
Although the SPI mold finish has established the standards for surface mold textures, some customers still refer to the old finish standards when they are making the mold finishing specifications. As an alternative, the Society of Plastic Engineers from the 1960s to 1980s created a scale of one to six to specify injection molding surface textures ranging from high-sheen diamond finishes to rough blasted surfaces.
Final Word
In plastic injection mold, the SPI standards on the molds have parameters. As a client, you must partner with an injection molding company that understands the SPI classification and can determine the right mold to produce the products that meet your requirements.