People often ask about several questions on liquid silicone rubber molding. It remains a silicone-oriented polymer that comes in two parts joined through the process of chemical bonding. If your quest is for the fabrication of injection crafted products, then using liquid silicone rubber molding is the best way to go. One advantage of using this process is that in the textile, consumer goods, food, and automobile industry, you can also make use of the technology.
There is a cross-link progression by the catalyst when the polymer remains heated and injection molded. There will be permanent shape and strength due to the progression occurring in the process after treatment. The end product will become durable, strong, and ensure that it can be used for designing O-rings, electronic interfaces, automobile parts, and appliance hardware.
Liquid Silicone Rubber Molding Produces Flexibility in Low Temperature:
When the temperature is extreme, there is a possibility for the flexibility of thermoplastic elastomers to fall during liquid silicone rubber molding. These elastomers may become highly brittle and harder that can later even crack at a low temperature. Even if the temperature is low up to minus fifty Celsius, liquid silicone rubber molding will always work. If you are producing products in an environment of low temperatures, it’s better to use this process.
The Chemical Resistance of This Production Process:
When considering several insight applications, thermoplastic elastomers have the capability of resisting chemicals during liquid silicone rubber molding. The truth is that these elastomers will also display these characteristics when the temperature range remains moderate. While remaining displaying great resistance to several chemicals, liquid silicone rubber can also provide low water absorption features at a low temperature.
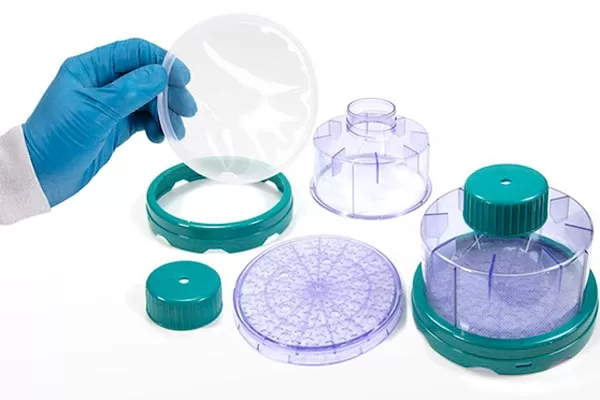
LSR products
Electrical Resistance in Liquid Silicone Rubber Molding:
There is the possibility for corona discharge to be resisted from the materials used by most electrical part manufacturers. With electrical stress, liquid silicone rubber will deliver a high resistance without affecting the conductivity of the end product. Due to this reason, the materials for liquid silicone rubber molding can be used in electrical parts and high-voltage applications.
Low Compression Model in Liquid Silicone Rubber:
What is the meaning of low compression models? Well, it’s the scenario that occurs making materials to have the capability of resisting permanent damage underneath a continuous strain. Within the range of fifteen to twenty percent liquid silicone rubbers often produce low compression models. When being compressed for a prolonged time, these materials have the capability to maintain their elasticity. Even subjecting these materials to several ranges of temperatures their elasticity will not be affected.
Another crucial thing to know about liquid silicone rubber molding is that the process comes with superior heat stability. If the temperature is up to one hundred and eighty degrees, these materials can always withstand the condition. Aging resistance is another feature you discover in this production process. Even excellent life reliability should not be ignored when using this manufacturing process. Using this process for fabricating parts and products will always be beneficial.