Rapid tooling and rapid prototyping are frequently used interchangeably in the manufacturing realm. What is the difference between the two and when is rapid tooling used?
Rapid Tooling refers to the process when rapid prototyping techniques and conventional tooling are used together to produce a mold quickly. The process also utilizes the parts of a model from CAD data at a fraction of the cost and time it takes to create a tool using conventional methods. It is also used as a way to produce injection molded parts.
How Does Rapid Tooling Work?
Rapid tooling refers to the rapid production of parts that function as a tool, mainly for mold inserts as opposed to being a functional part or prototype.
These tools are produced by various additive manufacturing techniques or rapid prototyping processes like stereolithography, fused deposition modeling, laser sintering, 3D printing, or electron beam melting. The tools are then used directly to create molds for conventional manufacturing like vacuum casting.
Rapid tooling is categorized into two different types: Soft and Hard, Direct and Indirect. And the wide range of materials in tooling includes wood, wax, photopolymers, thermal polymers, metals, ceramics, and composites.
In soft tooling, molds that are produced directly or indirectly are destroyed after a single cast is used in small batch production. The single cast is usually investment casting and the parts produced have identical properties to that produced through conventional investment casting. Furthermore, soft tooling is commonly used for low volume production when the demand is more concerned with application testing.
In hard tooling, the molds are produced using metals, ceramics, or composites and are used for high volume production. To put it in perspective, the metal molds and silica sand molds are produced directly using SLM or SLS techniques. The parts manufactured from these molds are of high quality, with fine finishing, and far more superior than the parts manufactured through conventionally produced molds. It can also produce highly complex molds.
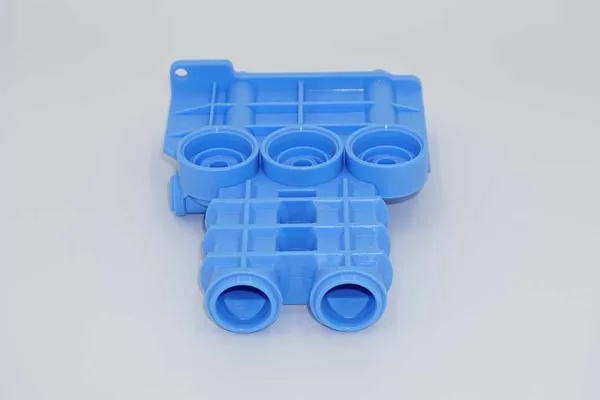
Plastic prototype part
What are the Benefits of Rapid Tooling?
Rapid tooling has several benefits, but the most evident is in cost savings. It greatly reduces the time needed to develop molds and speeds up production. Since you will have a shorter timetable, it allows companies to have better profits.
Rapid tooling also allows for ease of customization because of its flexibility in tool design, the capability of adapting to the customer’s specifications, and will not require a high volume to break even.
Conceptual designs can also be improved without further incurring additional costs compared to conventional manufacturing processes. All of these contribute to high-performance manufacturing and better quality products.
What to consider when choosing the rapid tooling process?
How do you know which type of rapid tooling to use? The answer depends on the product and at what stage you are in the design process. The company can make tooling recommendations based on several factors unique to your project. It includes:
- Timeline
- Budget
- Design complexity
- Materials
- Tolerances
- And many more
You can rely on engineering experts to carefully assess your situation according to these factors and recommend the most appropriate type of rapid tooling for your product.