For the purpose of creating parts for a number of industries and applications, plastic injection molding might be a practical technique. Plastic injection molding has been used as a stable production method for almost a century. Injection molding offers great design flexibility at an affordable price and is ideal for both basic, low-cost components and products requiring complex compositions and high tolerances.
Plastic Injection Molding Basics
The fundamental injection molding processes are identical for all parts. A hollow mold that has been filled with molten plastic resin is first used to construct the desired item. This tool is placed within an IMM(injection molding machine), sometimes referred to as a press, which manages the process of creating the object it holds. Click on the form throughout every cycle of each process to finish the necessary steps. The hard thermoplastic resin is melted and turned into a liquid when the press cylinder is heated. A liquid resin is subsequently injected by the cylinder into the casting cavity.
After being constructed, the press keeps exerting pressure on the molded part’s cavity in order to completely fill the resin. The resin hardens into a hard plastic when the item is finally cooled to the proper temperature. The completed product can be taken out of the mold and recovered before the subsequent molding cycle. The procedure can be repeated to produce tens, hundreds, thousands and even millions parts in production after the material has been processed to produce usable pieces.
A number of variables affect how much die-cast parts cost. The most important factors to take into account are the cost of the resin required for each component, the size needed to make the part, and how each part will be finished in the press.
A set of performance criteria, which may include functional characteristics, environmental and chemical compatibility, is frequently the foundation of material standards. Depending on their requirements, manufacturers can choose between varieties of resins, from affordable injection solutions to intricate, application-specific designs.
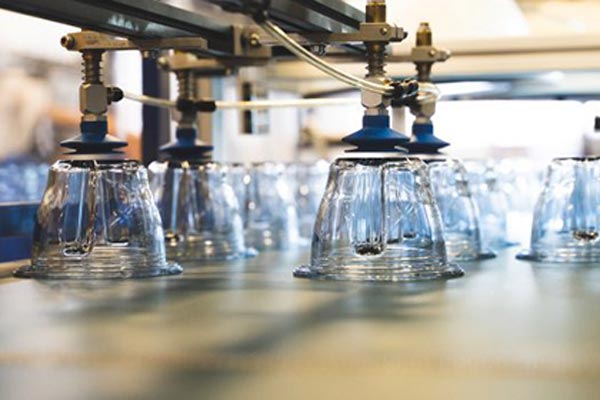
Custom plastic parts
Size and shape of a part are influenced by the amount of compression and cycle time needed to produce it; larger parts frequently require larger presses. One of the main advantages of plastic injection moldings, once these specifications are established, a substantial amount of symmetrical diversity can be added without having an impact on the part’s price.
Frequently, numerous old products are combined into one new casting to produce a new casting with significant cost savings. Manufacturers of parts can build a reputation for creating well-formed parts. These conventional authorities offer guidance on the design elements like wall thickness, object size, and the size of design components. Die casting machines commonly supply data for manufacturing (DFM) and components to guarantee compatibility for a specific molding application.
In order to create the component appropriately, many things must be taken into account, including material choice, part design, mold choice, and press choice. Before creating a new product, it is essential to understand how these components interact and control them to ensure that part manufacture goes as smoothly as is practical. Another crucial step in identifying potential part risks is mold modeling.
Producers can use this computer predictive analysis to inspect product molds and components to see whether an item is correctly packaged and wrapped.