Injection molding is a common process for producing plastic components and thermoplastics are used to produce the majority of molded plastic parts. On the other side, injection molding can be utilized to produce items from thermoplastic materials like LSR(liquid silicone rubber). Another great method for creating flexible parts, effects, and temperature components is known as liquid silicone injection molding.
Two-part silicone solutionsare combined before molding, with one half containing platinum to harden the silicone. Liquid silicone moldingenables manufacturers to produce a wide range of practical components for anextensive range of applications, including gaskets, kitchen cabinets, over-the-counter products, and more.
High quality, high injection molding productivity, and liquid silicone rubber elastomer properties are all advantages of LSIM(liquid silicone injection molding). Across a broadarray of industries, producers employ plastic injection molding. Because they are durable, lightweight, and simple to mould into a desired shape, plastics are widely used.
On the other hand, materials like thermoplastic-based elastomerscan’t withstand high temperatures and would melt losing their shape if exposed to them. Many manufacturers are switching to liquid silicone as a result.
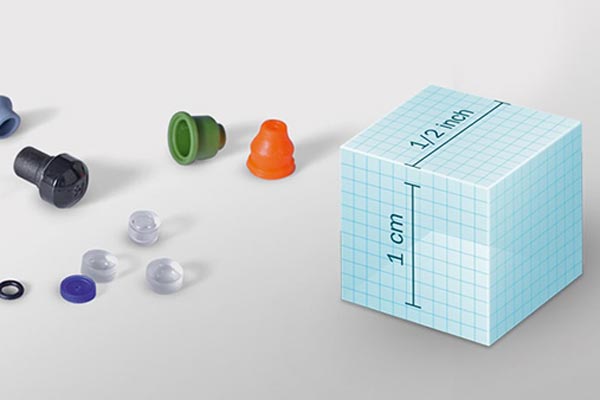
LSR injection molding parts
What is liquid silicone?
Based on silicone, the chemical LSR (Liquid Silicone Rubber) was created. Die-cast components are often used in the production of products for sectors like automotive, food, appliance, textile, and consumer goods.
As soon as the polymer is produced and then heated, a catalyst starts to move. This gives the body long-lasting strength and form after a demanding process.
What advantages does liquid silicone rubber offer?
1. A high tolerance for temperature
180 °C can easily be tolerated by LSR without melting it. They are now a widely used substitute for gaskets in the heavy-duty automotive industry.
2. Slight temperature change
Thermoplastic elastomers may become rigid at high temperatures. Low temperatures cause them to toughen and become more brittle, eventually exploding. The lowest temperature that LSRs can sustain is -50 °C. This is an excellent option for any product that needs to operate at low temperatures.
3. Age-defying properties
When choosing the ideal material for injection molding, aging resistance is a critical factor to take into account. Hardened LSR materials are extremely resistant to UV rays, aging, and weathering. They are appropriate for conditions where prolonged contact with the chemical is necessary.
4. Resistance to Chemicals
Thermoplastic elastomers are resistant to chemicals in many applications. They do, however, have great temperature tolerance and a poor chemical resistance. LSR has less water absorption even at high temperatures and is very resistant to common chemicals.
5. Strictly Condensable
Low compressibility materials can withstand ongoing deformation when subjected to constant force. LSRs have a low compression ratio, typically between 15% and 20%. They can maintain flexibility even after being blended for a long time and exposed to different temperatures.
6. Wide strength spectrum
The endurance of LSR is probably the most crucial factor affecting how simple it is to utilize in a production environment. Most Liquid Silicone Rubber products have a shelf durability of up to one year.
7. Electrical voltage immunity
Manufacturers of electronic equipment must be aware that any materials they use may withstand and becorona dischargeable. LSR delivers superior electrical voltage immunity without impairing the performance of the finished product. As a result, these materials are frequently used in contemporary electrical machinery and parts.
Consumer electronics to high-strength industrial uses are all included in the vast variety of applications of Liquid Silicone Rubber. Optics, automotive, electronics, consumer products, healthcare, and medicine are also a few of these. Due to the tooling flexibility and design, LSR injection molding is appropriate for producing intricate geometries and may incorporate numerous functional parts into a single product. LSR offers significant benefits when it comes to product reliability and overall tooling costs.