Blow molding and pressure die casting are distinct manufacturing processes, each with unique strengths. Blow molding excels at creating hollow plastic parts, while pressure die casting produces precise metal components.
However, combining these technologies opens up exciting possibilities for hybrid manufacturing. This approach allows you to create innovative products with enhanced functionality and performance.
Integrating Blow Molding and Pressure Die Casting
Integrating blow molding and pressure die casting allows you to combine the advantages of both processes. This leads to the creation of parts that would be difficult or impossible to manufacture using a single method.
Here are some examples:
- Plastic Bottles with Metal Inserts: Imagine a plastic bottle with a pressure die-cast metal thread for a more durable and secure closure.
- Hollow Metal Components with Plastic Features: A pressure die-cast metal housing can be combined with a blow-molded plastic cover to add ergonomic grips or functional features.
- Lightweight Structures: Combining lightweight blow-molded plastic components with structural pressure die-cast metal parts can create strong yet lightweight assemblies.
These hybrid designs offer unique solutions for various applications, from consumer goods to automotive components.
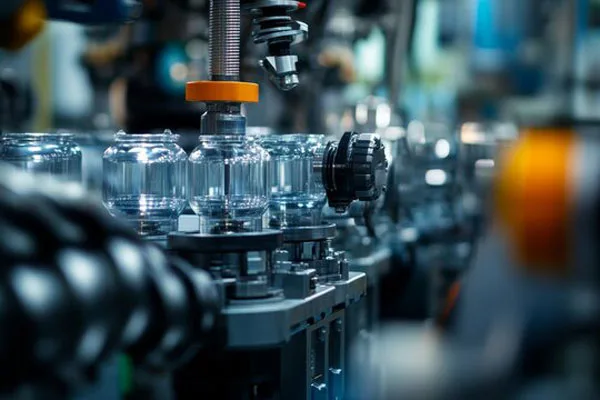
Blow molding process
Combining Blow Molding and Pressure Die Casting
Creating hybrid parts typically involves a multi-step process:
- Pressure Die Casting: The metal component is produced first using pressure die casting. This ensures precise dimensions and intricate details.
- Mold Preparation: The pressure die cast part is then placed into a blow molding mold. The mold is designed to accommodate the metal insert and create the desired plastic shape around it.
- Blow Molding: Molten plastic is extruded into the mold, encompassing the metal insert and forming the final part.
This process requires careful coordination between the two manufacturing methods to achieve accurate alignment and strong bonding between the metal and plastic components.
Advantages of Hybrid Manufacturing
Combining blow molding and pressure die casting offers several benefits:
- Enhanced Functionality: Integrate metal and plastic components to create parts with improved performance and features.
- Light weighting: Use lightweight plastics in conjunction with strong-pressure die-cast metal parts to reduce overall weight.
- Design Freedom: Expand design possibilities by combining the strengths of both processes.
- Cost-Effectiveness: Optimize material usage and reduce assembly steps by creating integrated parts.
This hybrid approach allows you to achieve design objectives that may not be possible with a single manufacturing method.
Applications of Hybrid Manufacturing
The applications for hybrid blow molding and pressure die casting are diverse and growing:
- Automotive: Create lightweight structural components, door handles with integrated electronics, and fuel system parts.
- Electronics: Produce housings for electronic devices that combine the strength of pressure die-cast metal with the design flexibility of plastic.
- Consumer Goods: Manufacture products like bottles with secure metal closures, toys with moving parts, and appliances with integrated handles.
As the demand for innovative and multifunctional products increases, this hybrid approach will become even more prevalent.
Future Trends in Hybrid Manufacturing
The future of hybrid manufacturing with blow molding and pressure die casting is promising. We can expect to see:
- Increased Automation: Automation will play a key role in streamlining the production process and improving efficiency.
- Advanced Materials: The use of new materials, such as bioplastics and high-strength alloys, will further expand design possibilities.
- 3D Printing Integration: 3D printing can be used to create complex molds for both pressure die casting and blow molding, enabling rapid prototyping and customization.
By embracing these trends, manufacturers can leverage the full potential of hybrid manufacturing to create innovative and high-performing products.
Blow molding and pressure die casting, when combined, offer a powerful approach to manufacturing. This hybrid method allows you to create unique parts with enhanced functionality, lightweight potential, and expanded design freedom. As technology continues to advance, we can expect to see even more innovative applications of this versatile manufacturing approach.