Silicone rubber is known for its excellent chemical inertness, a wide range of available durometers, toughness, flexibility, and ample operating range. It’s because of these reasons why many industries find it very helpful to them. The medical device industry is one of them. The ability of the material to withstand steam, ETO, UV sterilization, excellent biocompatibility, as well as low toxicity which makes silicone rubber as the perfect material in manufacturing parts of the medical device.
This industry should be able to determine which is best for their product – liquid silicone rubber (LSR) or high-consistency rubber. The mechanical characteristics and performance of both types are quite the same; choosing between LSR and HCR will depend on how the component will be built.
High Consistency Rubber (HCR)
The HCR is manufactured as gummy, with high-viscosity of varying thickness that is slightly vulcanized. Because of this, it is best for compression and transfer molding and also for extrusion. Manufacturing parts using HCR needs to undergo different steps, which makes it labor-extensive – mill softening, extrusion/molding, preform preparation, vulcanization, and finishing.
You can use HCR in injection molding, but because of the material’s high viscosity and long curing time, it takes a longer time to complete the cycle, and it is not practical at all. Because the fabrication methods rely on HCR, it produces a lot of waste material, needs more floor space, tools may incur high labor costs and equipment to complete the steps. Take note that equipment costs less than the steep design and the cost of machining needed by the LSR injection molding process.
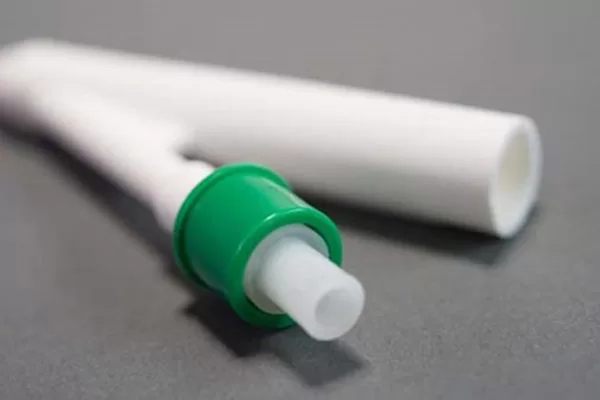
LSR injection molds
Liquid Silicone Rubber (LSR) – Best for Injection Molding
Liquid silicone rubber molding, on the other hand, starts with a two-part liquid that solidifies when combined together. Mixing is done using a metered mixer that accurately combines the two parts as in 1:1 ration before pumping the fluid into the mold, which is then heated to hasten the vulcanization process.
The combined LSR is forced into the mold under pressure. In liquid silicone rubber molding, low viscosity will lead to a quick mold fill as well as pack time, while the increase in mold temperature ensures short curing time. Since the curing time occurs inside the mold, there will be less material wasted as compared to high-consistency rubber.
The reduction in waste is due to the cold runner or cold drop tooling. It can be reduced even further by the liquid silicone rubber cold inside the runners and sprue. This only means that vulcanization only takes place inside the hot part cavities, which lead in no LSR lost to runner and sprue volume, and no further step of trimming is required.
Liquid silicone rubber molding produces consistent components, cycle to cycle. Also, the LSR process can reproduce complex and intricate shapes because it has a low viscosity that allows the material to fill the smallest spaces. And since it is a highly-automated process, it requires less labor to manufacture large quantities of parts, making liquid silicone rubber molding the best choice for high-volume manufacturing.