CNC machining has been growing in popularity in the manufacturing industry for several years. The shocking truth is that with this production technology, it has been easy to design and create several parts or products. Using the CNC machining process will help save producers a lot of time, energy, and money. For this reason, this article will be delving into something new today blind holes. Many people cannot still understand the mystery and details of a blind hole in machining.
What is the link between CNC machining and blind holes?
It’s crucial to know that the material will now the penetration of blind holes. It simply means that blind holes don’t have the capability to move through any production material. Due to this condition, chips designed during tapping, reaming, drilling, or other applications will not simply fall off. The only way to get rid of blind holes is by using several other means or simply employing cutting tools with helix. With this idea, you’ll discover that hole tapping is now simpler than a blind hole option. In this case, people may experience the breaking of taps than before. It’s at this juncture that you need the CNC machining techniques to handle things professionally.
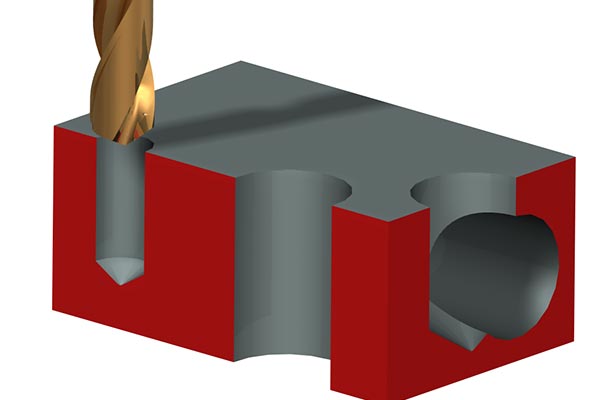
Blind hole tapping secrets
Using the perfect tap by employing the service of a CNC machining professional:
When talking about blind hole tapping in the CNC machining process, chips have no other option than to move in an upward direction. Chips will not be able to drop out easily because the hole comes with a solid bottom. On this note, it’s crucial when creating blind holes to make use of taps. In most cases, people keep asking a common question when dealing with blind holes.
What is the best tap to get when working on blind holes? Well, the best way to go on this issue is by seeking to create a bottoming tap. Without any doubt, the technology is old as far as CNC machining is concerned. The truth is that people should not worry themselves too much about bottoming taps. It’s because the additional threads that you find on these taps will not reach the lower part of the hole. If you’re planning for manual tapping applications, then you can care much about bottoming taps.
Selecting the perfect hole size to get started:
The first step that people have to follow when talking about this entire process is by picking the perfect hole size. One amazing thing that will shock anyone is understanding that the recommended size happens not to be the best. The normal thing to do is to ensure that the size you select creates a perfect balance of the required torque and the holding strength of the threads to tap. Remember that the force on the tap remains the torque and can break the entire system if it’s too much. Saving taps can be done by reducing the torque.
Why use blind holes?
There are a plethora of reasons to use blind holes in the CNC machining process. It can help prevent the loss of special taps from the bottom of certain machines. With blind holes, you can discover the value of taps and how they operate. On this note, understanding the secrets of blind holes will always help you to profit more.