Compression molding is a widely used manufacturing technique. It’s a similar process to plastic injection molding but with seamless fabrication that’s highly economical for producing parts at scale. Compression molding involves preheating material, known as the “charge,” before placing it in a cavity mold and compressing it under pressure to create a finished product.
Compression molding offers many advantages over other production techniques. It’s ideal for producing large components with complex designs in plastics or composite materials. While it’s an old fabrication and rapid prototyping technology, it’s still popular due to its high-efficiency level.
A wide range of compression molded products is featured in all industries, from aerospace parts to kitchenware. This post looks at compression molding applications in life.
What Is Compression Molding & How Does It Work?
This manufacturing process applies pressure and heat to material in a mold to shape a product. Compression molding is suitable for materials like thermos-setting and thermo-softening composite plastics and silicone.
The process utilizes a vertical press and heated cavity to produce the part, with easy maintenance of the tooling. It’s an ideal process for prototyping and mass production, with low-cost tooling keeping project expenses to a minimum.
Compared to injection molding, compression molding produces less waste. No gates, runners, or sprues are needed to form the product. Compression molding creates highly aesthetic and functional components with a superior smooth finish. It’s the ideal manufacturing technique for large curved and flat component manufacturing.
Compression molding is favorable to other manufacturing processes when shaping composite materials with stiff, durable, and corrosion-resistant properties. The most common types of materials used in compression molding tasks include mixtures of thermoset and bulk molding (BMC) or sheet molding compound (SMC).
As with all other manufacturing techniques, compression molding isn’t a perfect process, and there’s room for error. Producing highly intricate parts might also be challenging, and the process takes longer than other rapid prototyping and manufacturing techniques.
Finished parts can separate from the mold with “flash” on the seams, which requires trimming and extra labor costs.
Preparing the raw materials for molding is the first step in the compression molding process. The materials come in the form of pellets, powder, or pre-forms. The operator preheats it, placing it in the mold cavity. Compression molds feature design and construction with aluminum or steel.
After loading the material into the mold, the operator seals it with the matching top of the mold and closes it with a hydraulic press. The press’s vertical compression forces the charge to fill the mold uniformly, creating the part.
During molding, the mold remains closed, and the high temperature cures the plasticized charge material, forcing it into the mold’s shape. After the curing process ends, the operator separates the mold, removes the part, and trims the flashing.
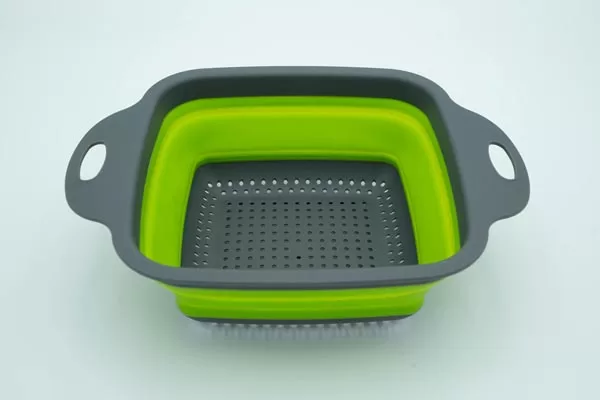
Silicone folding basket
Common Industry Applications for Compression Molding
We use compression-molded parts every day, and most of the time, they go unnoticed. Here are some industries and common products that feature compression molding in prototyping or manufacturing projects.
Automotive
Compression molding is vital for producing spares in the automotive industry. Compression molding allows for the fabrication of lightweight parts, improving vehicle fuel efficiency. Plastic composites like GFRP and CFRP are featured in car components like bumpers, door panels, and dashboards. The technique also forms mechanical and electrical components throughout the vehicle’s design. Rubber is a common material used in the fabrication of O-rings, dampening boots, and other vibration-resistant and water-resistant components.
Aerospace
The aerospace industry utilizes compression molded parts featuring composite materials to improve the strength-to-weight ratio of finished parts. The industry uses several materials in compression molded parts, including carbon fiber-reinforced plastics (CFRP) and fiberglass-reinforced plastics (GFRP). These materials are molded into components like blades, wings, and engine casings.
Electronics
Many electronic products feature manufacturing with compression-molded components. Cellphones feature compression molded casings, and many laptop chassis are compression molded. Compression molding allows for the production of complex plastic parts with a greater degree of intricacy than injection molding.
Medical
The medical industry has stringent quality standards on medical devices and other plastic products used in hospitals and medical facilities. Compression molding allows for repeatable quality, and it’s a popular manufacturing method for producing diaphragms, orthopedic surgical implants, vibration inhibitors, CPAP masks, and cylinder lip seals.
Alternate Industries
Compression molding is also featured in rapid prototyping and mass manufacturing in many other industries. Other examples include machinery components and bearing bushes in the mining and oil and gas industries and wear plates and chain guards in agricultural equipment.
Wrapping Up
Compression molding is a popular prototyping and manufacturing method across many industries. It’s a good choice for development projects due to its capability of producing components with high tensile strength capable of withstanding harsh environments. It’s ideal for low or high-volume production projects and is one of the lowest-cost options.