Compression molding has been around for a while, but it’s experiencing a resurgence in popularity thanks to the rise of composite materials. These advanced materials are changing the game in industries like aerospace, automotive, and renewable energy, demanding manufacturing processes that can keep up. That’s where compression molding shines. Let’s take a closer look at how this process is shaping the future of composites.
Compression Molding Meets Advanced Composites
Composite materials are basically superheroes in the world of materials science. They combine the strengths of different materials to create something entirely new and often superior. Think carbon fiber, fiberglass, and other high-performance materials that are stronger, lighter, and more durable than traditional options.
But working with these advanced composites requires specialized manufacturing techniques, and that’s where compression molding comes in. This process involves placing a preheated composite material (often in sheet form) into a heated mold cavity. The mold is then closed, and pressure is applied, squeezing the material into the desired shape and curing it in place.
Compression molding is particularly well-suited for composite materials because it can handle complex shapes, intricate designs, and large parts. It’s also great at producing high-quality parts with excellent surface finishes and dimensional accuracy.
Benefits of Compression Molding
- Weight Reduction: Composite parts produced through compression molding tend to be lighter than their traditional counterparts, reducing material costs and energy consumption.
- Enhanced Strength: Compression-molded composites exhibit superior mechanical properties, such as tensile strength, fatigue resistance, and impact resistance.
- Improved Sustainability: By using eco-friendly materials and minimizing material waste, compression molding contributes to a more sustainable manufacturing future.
- Increased Design Freedom: Compression molding’s versatility and flexibility enable designers to push the boundaries of part design and functionality.
Compression Molding in Aerospace
The aerospace industry is always looking for ways to make aircraft lighter, stronger, and more fuel-efficient. And guess what? Compression molding with composite materials is a key enabler of these advancements.
From wing components and fuselage panels to interior parts and engine components, compression molding is used to create a wide range of aerospace parts. These composite components offer significant weight savings compared to traditional metal parts, which translates to improved fuel efficiency and reduced emissions.
Plus, composite materials offer excellent strength and stiffness, making them ideal for withstanding the stresses and strains of flight.
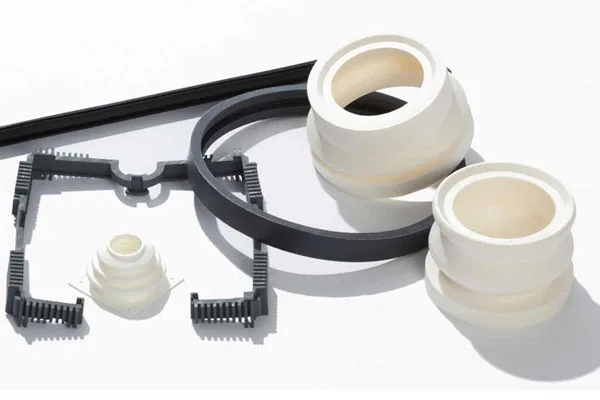
Compression molding parts
Compression Molding in Automotive
The automotive industry is another hotbed for compression molding with composite materials. As car manufacturers strive to meet stricter fuel efficiency standards and reduce emissions, they’re increasingly turning to lightweight composite parts.
Compression molding is used to produce a variety of automotive components, including body panels, bumpers, dashboards, and structural parts. These composite parts not only reduce vehicle weight but also offer improved crashworthiness and durability.
Moreover, compression molding allows for greater design flexibility, enabling the creation of complex shapes and aerodynamic features that improve vehicle performance.
Compression Molding in Consumer Goods
In the ever-evolving landscape of consumer products, manufacturers are constantly searching for ways to enhance product performance, reduce environmental impact and meet consumer expectations for aesthetic and functional design. One of the key technologies driving these advances is compressive molding with composite materials.
Compression molding is used to produce a diverse array of consumer products, from sports equipment and electronics housing to furniture and home decor. The adoption of composite materials in this manufacturing process provides substantial benefits that cater to the demands of modern consumers.
Compression Molding in Renewable Energy
Renewable energy technologies like wind turbines and solar panels rely heavily on composite materials. And you guessed it – compression molding plays a vital role in their production.
Wind turbine blades, for example, are often made using compression molding of composite materials. These blades need to be incredibly strong and lightweight to withstand the forces of wind and maximize energy capture.
Similarly, compression molding is used to create structural components for solar panels, ensuring their durability and longevity in harsh outdoor environments.
Optimizing the Compression Molding Process
As the demand for composite parts grows, so does the need for efficient high-volume production methods. Fortunately, compression molding is well-suited for this challenge.
By optimizing process parameters like temperature, pressure, and cycle time, manufacturers can achieve high production rates while maintaining excellent part quality and consistency.
Automation and advanced process control systems further enhance efficiency, reducing labor costs and minimizing waste.
Compression molding is a key enabler in the composites age, providing a reliable and efficient method for producing high-quality parts for a variety of industries. With its ability to handle complex shapes, large parts, and high-volume production, compression molding will continue to play a crucial role in shaping the future of composites.