Manufacturers across the different industries from fire protection to healthcare, automotive, or other transport sectors need easy to mold or demold rubber silicones. It needs to be done as efficiently and as cost-effective as possible.
One of the requirements in making these products are fillings for mold that remains stable in the direct injection systems and other automated processes. It also needs products with specific properties like fast curing or “flashless” technology that is achieved upon the addition of additives to adapt to a variety of molding processes.
Rubber
One material meets all these requirements: liquid silicone rubber. It is made of two components, the catalyst, which is typically platinum-based, and a coloring paste. Because of its low viscosity index, LSRs need perfect seals in the parting line and mold cavity that guarantees a burr-free finished part.
Liquid silicone injection molding is the process of using LSR to produce a wide range of consumer goods, medical devices, automotive parts, and other items. Although this manufacturing technique is well-known, there are persistent misconceptions about the process, which prevents businesses from taking advantage of its benefits.
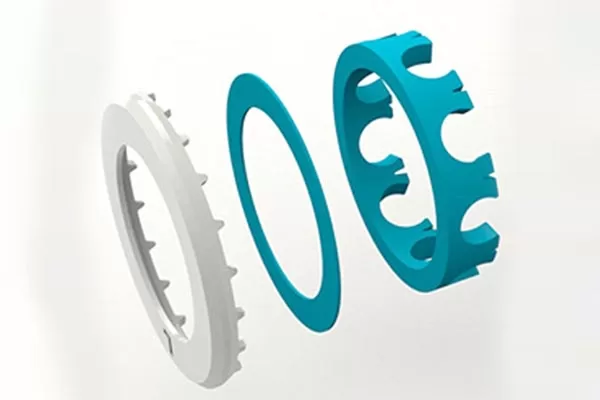
Custom plastic parts
Common Myths About Injection Molding
Many manufacturers have misconceptions about the liquid silicone injection molding process. Here are some of the most common myths about it.
It has limited capabilities
This is not true. Injection molding is a broad category that encompasses a wide range of materials and processes. The products from the injection molding process can range from simple to technically and dimensionally complex due to the elasticity of the material. This allows for undercuts and different wall thicknesses.
It is expensive
Another myth about silicone injection molding is that this process is expensive. It is the opposite, as injection molding can be cost-effective when used in high-volume production. The process has fast cycle times, so it has a high output. Other than that, liquid silicone injection molding has no material waste, and there is no cost for additional processes like deflashing.
It requires longer lead time and replacement tooling
The mold used in silicone injection mold has to be precise and of high quality. It can range from thousands of millimeters instead of hundreds, and as such, there are lots of tool adjustments and optimization to be done. This explains the length of time it takes to complete the mold. It needs experienced toolmakers to complete a mold that can run for more than a thousand shots.
Getting the Facts Straight
After debunking the myths about silicone molding, here are some facts to keep in mind.
- Liquid silicone rubber injection molding can be a versatile solution for making parts that you may not think possible.
- Liquid silicone rubber injection molding can be a cost-effective option both for low volume and high volume production.
- Liquid silicone rubber injection molding can run for a very long time using the same mold.
Conclusion
Now that you have a clear understanding of silicone molding, you can now use this process to your advantage. It can promote the rapid production of products that fulfills the features you need.