Die casting is the quickest and most economical forming process in the manufacturing sector. One of its advantages is that the production process can create from hundreds to thousands of parts using only a single mold. All these parts have the same quality and consistency at a relatively low cost per unit.
In this article, we are going to discuss how the manufacturing process looks and what are the materials that can be used in die casting.
Die Casting Defined
Die casting is a fully automated casting process where the liquid material is poured into a mold at very high pressure (from 150 to 1200 bar) and at a high filling speed. The alloy used in die casting should have a low melting point. You can imagine how fast each die-casted part is made.
The casting process is perfect for components that require high volume and are made in a series because the molds are not destroyed after the casting process. With die casting, it is possible to manufacture large and complex parts with thin walls that other processes can do.
The molds used in die casting the mold are exceptionally strong. It is made from high-quality and heat-resistant steel grades in two haves forming a cavity. This is where the liquid metal is pressed during the casting process. The halves are found on a fixed and movable plate and during production, pressure is applied to these molds.
In some cases, the mols are heated and cooled to achieve a certain solidification required for the part. The molds used in die casting are expensive but they can make thousands if not millions of parts with just one piece.
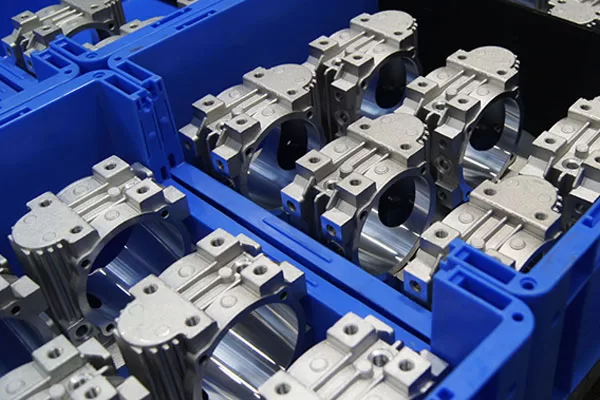
Die casting products
Alloys in Die Casting
There are three main alloys used in die casting: aluminum, zinc, and magnesium. These metals are non-ferrous and have mechanical properties that are compatible with the parts needed to be cast. They not only possess the properties the manufacturers need like operating at high temperatures, but these alloys are also fully recyclable.
- Here are the requirements for alloys for die casting:
- High tensile strength
- High electrical and thermal conductivity
- Great corrosion resistance
- Outstanding EMI/RFI protective properties
- Good finishes
The Die Casting Process
In die casting, every project has its needs. You can find several companies that offer different types of the casting process. In general, there are three types of die casting processes:
- Hot Chamber: For zinc and some magnesium alloys that do not erode the metal pots, plungers, and cylinders.
- Cold Chamber: It is best for alloys that have high melting points like aluminum. During the process, the metal is in a liquid state and then put into the cold chamber with hydraulically operated plungers to push the material into the die.
- Injected Metal: As the name implies, it is an innovative version of die casting where there is only one step involved in the process. It is used for small components and contributes to reducing manufacturing costs.
Fields of Application
The die casting process is used mainly in industries that require large components like automobiles and aerospace. But it is also used in manufacturing domestic appliances, furniture, power tools, electronics, types of machinery, and lighting systems.