Liquid silicone rubber molding has gained significant attention in recent years due to technological advancements and evolving market demands. This process continues to transform various industries by offering innovative solutions for complex manufacturing challenges.
In this blog, we’ll explore the latest trends and innovations in liquid silicone rubber molding that are reshaping how products are designed and produced.
Advancements in Materials
Recent breakthroughs in LSR molding have introduced advanced materials with enhanced properties. These include:
- Reinforced LSR: The incorporation of fillers like glass fibers significantly increases the strength and durability of LSR, making it suitable for demanding, high-stress applications.
- Thermal Conductive LSR: This specialized silicone facilitates efficient heat dissipation, a crucial feature for electronic components and devices that generate heat.
- Self-Healing Silicone: Cutting-edge innovations in molecular design have led to the development of self-healing silicone. This remarkable material can recover from minor damages, extending the lifespan of products and reducing waste.
These advanced materials expand the possibilities of LSR molding, enabling the creation of smarter, more durable, and higher-performing products.
Automation and Smart Manufacturing
The integration of automation and smart technologies is revolutionizing LSR molding:
- Robotic Automation: Robots are increasingly used in the molding process to improve precision, reduce cycle times, and enhance overall efficiency. They can handle tasks like material handling, assembly, and packaging, freeing up human workers for more complex tasks.
- Smart Sensors: The incorporation of sensors into molding equipment allows for real-time monitoring of critical parameters like temperature and pressure. This data-driven approach ensures consistent quality, minimizes defects, and reduces waste.
- AI and Machine Learning: Predictive analytics and machine learning algorithms are being leveraged to optimize production schedules, material usage, and energy consumption. This leads to cost savings, improved resource efficiency, and reduced downtime.
These advancements position LSR molding at the forefront of smart manufacturing, enabling greater productivity, efficiency, and responsiveness to market demands.
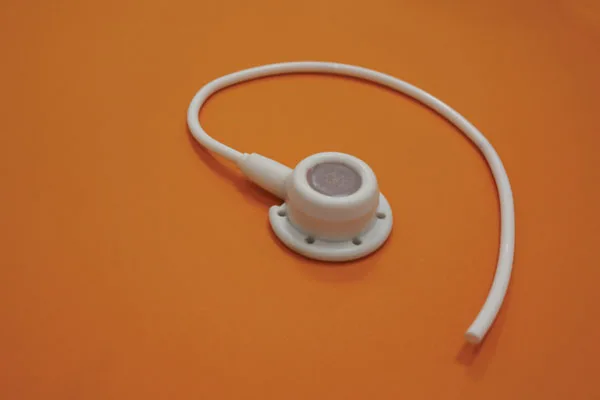
LSR medical devices
Sustainability Trends in Liquid Silicone Rubber Molding
Sustainability is a growing concern across industries, and liquid silicone rubber molding is no exception. Recent trends include:
- Bio-based Silicones: Manufacturers are exploring renewable resources to produce LSR, reducing dependence on fossil fuels.
- Recyclability: Innovations are making it possible to recycle silicone products, minimizing waste and environmental impact.
- Energy Efficiency: New molding technologies aim to reduce energy consumption during production, aligning with global sustainability goals.
By adopting these sustainable practices, the liquid silicone rubber molding industry is contributing to a greener future.
Customization and Personalization in Liquid Silicone Rubber Molding
Consumers today demand personalized products, and liquid silicone rubber molding is adapting to this trend:
- On-Demand Production: Technologies like 3D printing and rapid prototyping allow manufacturers to create customized silicone parts quickly and efficiently.
- Color and Texture Options: Innovations enable a wide range of colors and textures, allowing for unique product designs that cater to individual preferences.
This shift towards customization enhances user experience and satisfaction in various applications, from consumer goods to medical devices.
Conclusion
The future of liquid silicone rubber molding is bright, with ongoing innovations paving the way for enhanced materials, automation, sustainability, and customization. By staying informed about these trends, you can leverage the benefits of liquid silicone rubber molding in your projects, ensuring you remain competitive in a rapidly evolving marketplace.