Compression molding is a popular rapid prototyping technique involving a manufacturing process where preheated material expands inside a mold cavity, causing it to take the shape of the mold. Compression molding creates parts used in many industries, from automotive to aerospace.
It’s a cost-effective manufacturing process, but a lot can go wrong with it. It’s important for manufacturers to consider relevant factors influencing a successful outcome of the molded component before undertaking the task.
Materials Suited to Compression Molding
Materials used in compression molding have varying properties and characteristics that influence the performance and quality of the final product.
Flow rates and viscosity vary between materials, and the thermal conductivity of materials influences the warming and cooling rates.
Some materials may create more “shrinkage” during the molding and curing process. Manufacturers must take shrinkage into account when planning the mold design and dimensions.
Complexity & Geometry of Parts
Components with advanced design features increase the number of stages required in molding, influencing costs and manufacturing time.
Intricate design components may affect the flow of materials in the model under heat, resulting in defects or voids in the final product.
Mold Tooling Design
Mold design must consider material flow to mitigate the risk of producing defective components. The tooling must be capable of handling high temperatures and pressures during the molding process.
The tooling should be easy to maintain and repair, minimizing maintenance costs and downtime in production.
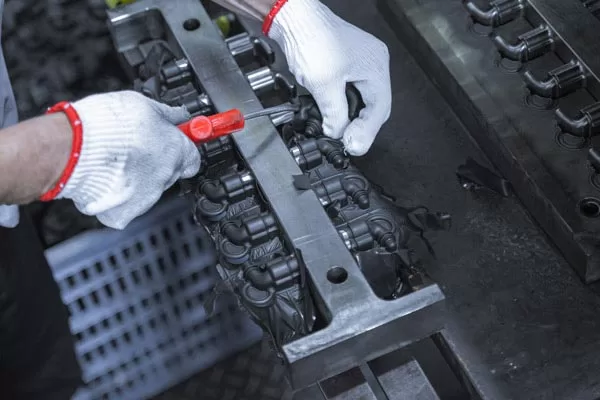
Silicone mold
Rib Design & Wall thickness
The rib design and wall thickness of the mold are critical considerations. If the mold walls are too thin, the final molded component is distorted and warped.
If the mold walls are too thick, it may result in voids or sink marks. Manufacturers must consider the material’s flow characteristics and components’ structural requirements when deciding on the right wall thickness for the mold.
The rib design in the mold affects the stiffness and strength of the mold. Correct rib design ensures consistent material flow in the mold and less risk of creating voids or sink marks in components.
Undercuts & Draft Angles
Correct draft angles are necessary for quick ejection of molded components from the mold. The draft angle must allow for the smooth release of the finished part without changing the details or texture of the mold.
Undercuts make it challenging to remove finished components from the mold. The mold design must include the correct draft angle and minimize undercuts to ensure clean, smooth component ejection after molding.
Mold Shrinkage
Mold shrinkage results in irregular dents in the joints of thick-walled cylindrical products, known as “cracking.” It’s a common issue in compression molded parts. There’s a difference between the vulcanization (curing) rate of surface layer rubber and inner rubber contacting the mold surface.
The pressure increases under thermal expansion as the internal rubber temperature rises slowly. This effect causes surface layer vulcanization by squeezing into the clamped surface, damaging the cured rubber at the mold corners.
To overcome this challenge, manufacturers must ensure an even temperature between the mold’s inner and outer material layers.
Heating and injecting the material into the mold cavity can overcome these problems. However, this process is challenging in compression molding, and the best way to mitigate this problem is to burr the mold corners and install a heat source in the core of the mold to keep it warm.
Uneven Surfaces
Inadequate dispersion of melt compounding agents at vulcanization temperatures can cause fine collapse in molded products. Materials must be thinned or filtered to eliminate unevenly dispersed additives in the compound.
As a result, the material viscosity decreases, and this effect changes its vulcanization properties. Mixing foreign substances or dissimilar materials also creates tiny pores in the vulcanized product.
Excessive mold cooling after heating or moisture absorption in the filler can cause pores to form in the product.
In this instance, it’s easy to contaminate the mold, and there is a greater chance of material scorching. This contamination affects the thermal aging and electrical insulation properties of the material.
Wrapping Up
There are several factors for manufacturers to consider when designing compression molding tooling and using it in low-volume production or rapid prototyping projects.
Material selection, part geometry, rib design, wall thickness, draft angles, and tooling design are just a few factors to consider when planning your project.
Ensuring you plan your rapid prototyping or low-volume production project creates successful results. Consider these guidelines to produce high-quality components and cost-effective prototyping and production runs.
Considering these factors during the planning phase ensures an optimized compression molding process. The process should produce final components that meet specifications if everything is in check.
That’s why choosing a production partner with experience in working with compression mold tooling and materials is crucial. Your production partner is a huge component in the success of your low-volume production or rapid prototyping project.