The prototyping process will not be as successful as it is today without the introduction of rapid tooling. This process allows product designers to create multiple prototypes quickly as opposed to using the conventional tooling means.
This is a good solution for many inventors, entrepreneurs, and businesses as it can be a quicker and more effective means of developing a new product from scratch. However, there is one thing that these stakeholders must know to take full advantage of its benefits, which type of rapid tooling to use.
There are two types of rapid tooling: direct and indirect tooling and each has its pros and cons. Some products can benefit from direct tooling while others from indirect tooling. To give you an idea of which option will be the best fit for your prototyping process.
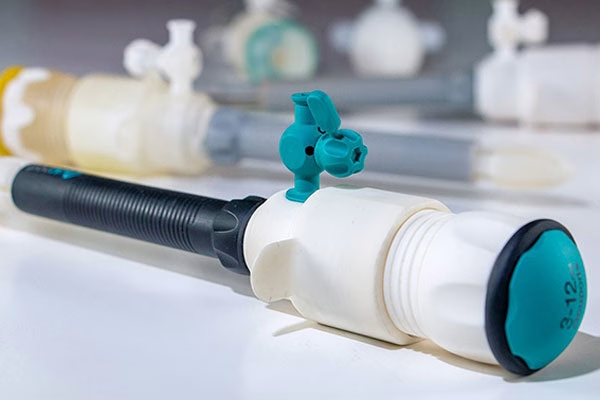
Rapid tooling services
Direct Rapid Tooling
Rapid tooling is the general term used to refer to any process where you can create a tool or mold in such a short amount of time. However, there is more to tooling than this definition. First, let us discuss direct tooling.
With direct tooling, the first step is to create a tool or mold through Computer-Aided Design software or CAD. This file will be sent to the printer or machine to create the actual mold or tool to be used in producing the prototype. You can also use a CNC machine, a subtractive process where the block of material is formed into shape from scratch. This tool can be used directly to make prototypes.
Direct tooling is usually more commonly applied to manufacturing than in prototyping. In low volume manufacturing rapid tooling is beneficial in creating molds quickly so that you produce products immediately. However, you can still use direct tooling for prototyping but with certain limitations.
For designers who simply want to test their designs as fast as possible, we recommend this type of tooling.
Indirect Tooling
The second type of rapid tooling is indirect tooling. The indirect tooling process is a bit more complicated than direct tooling but straightforward.
The first step in indirect tooling is to create a model for the master tool or mold with CAD software. Then, this file is sent to a machine or printer to create the master pattern. This master pattern is very durable and can be used to create multiple prototypes.
With the master pattern, you can create new mold and tools made from different materials. The master pattern is also applicable for either soft tooling or hard tooling and can produce many different tools or molds in small or large quantities with the same mold.
Indirect tooling is commonly used during the prototyping stage compared to other types of rapid tooling. These prototypes are meant for experimentation and testing. When the design is ready and designers want to test different materials, indirect rapid tooling is a great option to create multiple test tools and molds using the same pattern.
Conclusion
Which type of rapid tooling to choose? It depends on the product design and product use. If you create a design, and are still very early in the process, this is the best time to decide on which type of rapid tooling to use.