In the realm of mold making, innovation has always been a driving force, shaping the efficiency and quality of manufacturing processes. Liquid silicone for molds has emerged as a game-changer, offering a versatile and dependable material that addresses the demands of intricate designs and diverse applications. This article delves into the properties and applications of liquid silicone in mold making, highlighting its pivotal role in achieving precision and durability.
Flexibility and Detail:
Liquid silicone for molds, in contrast to traditional rigid mold materials, possesses remarkable flexibility. This inherent quality allows for the creation of molds that can capture intricate details and complex geometries with exceptional precision. Whether it’s fine textures, micro features, or elaborate designs, liquid silicone molds can reproduce them faithfully, making it a preferred choice for industries that demand high precision.
Ease of Use and Fast Curing:
Liquid silicone boasts a user-friendly nature, making it easy to work with during the mold-making process. The material typically has a low viscosity, facilitating the pouring or injection into mold cavities. Moreover, liquid silicone exhibits fast curing times, reducing the overall production cycle and increasing efficiency in mold fabrication.
Excellent Release Properties:
The non-stick properties of liquid silicone simplify the demolding process. Molds made from liquid silicone tend to release the cast parts effortlessly, minimizing the risk of damage to the final product and ensuring a smooth and efficient production workflow.
High Temperature Resistance:
Liquid silicone for molds exhibits impressive resistance to high temperatures, making them suitable for a wide range of applications. Whether used for casting molten metals, high-temperature plastics, or other heat-sensitive materials, liquid silicone molds maintain their structural integrity and dimensional stability even under extreme conditions.
Chemical Resistance:
The chemical resistance of liquid silicone for molds adds to its durability, ensuring that the molds can withstand exposure to various chemicals and substances used in different manufacturing processes. This property is particularly valuable in industries such as automotive and electronics, where harsh chemicals are commonly encountered.
Applications in Various Industries:
Medical Devices:
Liquid silicone for molds finds extensive use in the production of medical devices due to its biocompatibility, precision, and ability to create complex shapes. From intricate surgical components to soft-touch medical equipment, liquid silicone molds contribute to the production of critical healthcare products.
Automotive Components:
The automotive industry benefits from the versatility of liquid silicone molds in crafting components such as gaskets, seals, and intricate parts with tight tolerances. The material’s resistance to heat even chemicals makes it well-suited for the demanding conditions within automotive applications.
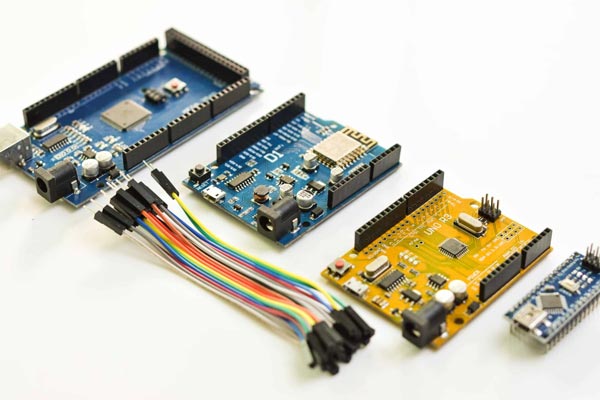
Silicone electronics devices
Consumer Electronics:
Liquid silicone molds play a crucial role in the production of components for consumer electronics. The ability to replicate intricate details and the material’s resistance to environmental factors make it ideal for creating keypads, buttons, and protective covers for electronic devices.
Customized and Artisanal Products:
Liquid silicone’s adaptability has found a niche in the production of customized and artisanal products. From bespoke home décor items to personalized accessories, craftsmen leverage liquid silicone molds to bring unique and intricate designs to life.
Liquid silicone for molds stands at the forefront of mold-making technology, offering a perfect blend of flexibility, precision, and durability. As industries continue to push the boundaries of design and functionality, the versatility of liquid silicone molds ensures they remain a cornerstone in the manufacturing process. From medical breakthroughs to artistic creations, the impact of liquid silicone for molds resonates across diverse sectors, shaping a future where precision and durability are paramount in the world of mold making.