There are plenty of ways to make a prototype, but if we are talking about the most cost-effective, then the answer would be vacuum casting.
In rapid prototyping, this manufacturing technique can complement other processes like CNC machining and 3D printing. It can also be used independently in creating high-quality prototypes for product development or end-use products in lean volume.
What is Vacuum Casting?
Vacuum Casting or sometimes referred to as urethane or polyurethane casting is a widely used technique that was first developed in Europe in the 1960s. From then, it became one of the most popular methods in creating plastic prototypes.
What sets vacuum casting apart from other prototyping means is its effectiveness and flexibility in creating high-quality prototypes and end-use products in low quantity. It is also faster than other manufacturing techniques.
Vacuum casting involves the use of pourable casting resins and reusable silicone molds. The mold can be used not more than 20 times to make exact replicas of the master patterns. The finished part is vital for engineering and functional testing in product development. It also creates parts for use as display models for stakeholders during approvals and marketing.
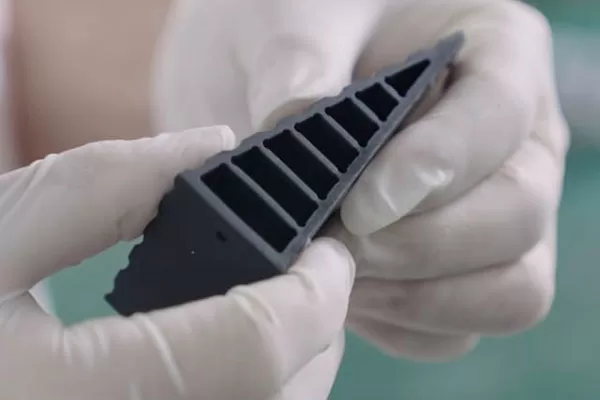
Vacuum casting parts
Why It is Good to Use in Rapid Prototyping
Today, it is normal to see vacuum casting is used in different stages of the prototyping process. Here are the reasons why.
Quality
The primary reason why you should consider vacuum casting as a prototyping technique is because of its quality. Even if it is a prototyping process, parts produced from vacuum casting are end-product quality, comparable to that of plastic injection molded products.
It is the vacuum casting process itself that creates such high-fidelity. Since the silicone molds are formed from master patterns, they can copy even the smallest detail. Therefore, vacuum casting is recommended for parts with detailed components.
Material Choice
Vacuum casting does not have limited material selection. The material of the master pattern is not relevant, and the mold is made from silicone alone. However, you can choose the material (polymer resins) during the final casting. These materials can resemble that of commonly used thermoplastics. That means that the prototype from vacuum casting is close to what would be the final product.
Testing
Since the vacuum cast parts are accurate and made from different materials, they can resemble the final part. This is suitable for testing and validation. This quality benefits the product designers because they can determine if the product is viable for the applications they have in mind. Most often, vacuum cast prototypes are used for fit testing, aesthetic and mechanical validation, and consumer trials.
Time
Prototyping needs faster turnaround time, and vacuum casting can help save time and speed up product development. There is no conventional tooling needed like injection molding because the silicone mold can be made in one day. Another advantage is it can be a great option for creating production-grade parts.
Cost
The last reason why vacuum casting is a preferred prototyping technique is that it is a less expensive way to manufacture high-quality prototypes in small batches before going into full production.
If you have questions about vacuum casting and the technique is right for your rapid prototyping requirements, call Nice Rapid. A representative will be glad to answer your questions.