Rapid prototyping is a core component of the design process and approval for mass manufacturing. The rapid prototyping process involves designing components in a virtual modeling process in Computer Assisted Design (CAD) systems.
Industrial companies may require the fast production of prototypes before moving into a short or medium-length production run. Prototyping components allows for testing and identifying changes needed to parts before finalizing mass production.
Customers use rapid prototyping projects to assemble a functional component or product for testing in the real world. Therefore, customers require an accurate representation of their design in the finished prototype.
The beginning defines the rest of the prototyping process. Accurately replicating that design is critical to the design approval process. To enable fast and efficient prototyping projects and the best chance of achieving success, you require reliable silicone molds, tested and proven to deliver accurate results.
Liquid silicone brings flexibility to liquid injection molding processes. The flame resistance and high heat resistance available with this material make it ideal for the molding process. Its physical properties allow it to withstand temperatures ranging from -130°F to 480°F.
As a pliable and highly malleable material, silicone molds allow for the coloring or transparency of finished components. Silicone molding is ideal for rapid prototyping projects in several industries, including the following.
- Automotive
- Medical
- Aerospace
- Defense
- Textiles
- Food
- Appliances
- Electronics
Companies can benefit from including silicone molding processes in their prototyping projects. It’s possible to use silicone and acrylics in the process. The spring-loaded nozzle prevents the machine from experiencing clogs or backups.
The process involves a plunger holding the forming plastic base, and the other has the catalyst. Both go into the static mixer, where it is injected into the mold at temperatures of 355°F. to 390°F. After it cures, the mold produces the near-completed component, bringing the materials back to the melting point, followed by a cooling period.
The cost, speed, and accuracy of the component design, including the material dimensions and properties, are critical criteria for selecting the right fabrication methods for silicone prototypes. There are more options for silicone parts than thermoplastics, adding challenges to the development process.
Available processes for manufacturing silicone prototypes include the following.
- Room Temperature Vulcanization (RTV)
- Fused Deposition Modeling (FDM)
- Selective Laser Sintering (SLA)
- Transfer Press Molding with High Consistency Rubber (HCR)
- Injection molding
Most silicone prototypes are manufactured using LSR, liquid silicone rubber. Most manufacturers use injection molding with material durometer ranges between 30 to 70 Shore A.
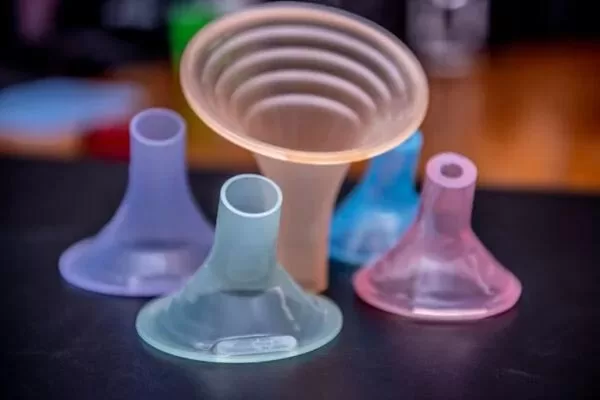
Injection molding products
A Review of 3 Common Methods for Making Silicon Molds
Injection molding, casting, and compression molding are the three primary methods used in silicone molding. The manufacturer offers the client a mockup of their finished prototype featuring sketches or handcrafted parts based on testing and concept refinement during the design process.
The manufacturer omits the details in the design at this stage of prototyping. The goal of this phase is to give an overview of the product. The next step is to create a working or rough prototype to create the final form of the component and settle on the materials for the project.
The final step is creating a functional prototype molded in the selected material with dimensional accuracy.
Here’s a brief overview of other mold prototyping techniques and the advantages and disadvantages of each.
RTV Molding
You find industrial RTV silicone formulations widely available, even from hardware stores in your local area. Manufacturing prototype parts from these materials requires a mold to create the final form.
Manufacturers build molds out of plastic or metal materials, depending on the project requirements and the type of materials used. However, it’s important to note that RTVs are cured at ambient room temperatures. However, manufacturers may use ovens to accelerate the curing phase.
Pros
- RTV is attractive for rapid prototyping projects since it doesn’t have the capital requirements of other solutions.
- There are plenty of options for materials.
- RTV molded prototype components are similar in accuracy to LSR components.
- It’s common for established and well-equipped R&D labs to have manufacturing abilities in-house to create tools from plastics and other soft materials.
- After manufacturing the mold, making components is a user-friendly fill-and-wait process.
- Depending on the project requirements, skilled technicians can make a prototype component in a single day.
Cons
- RTV prototype molding is a slow process, and curing times on finished components can last anywhere from minutes to hours.
- The processing time determines the cost per piece and production rates.
LSR
Liquid Silicone Rubber involves injection molding and production-grade materials molded for use in soft metal tooling.
Pros
- Fast part production due to fast-tracked tooling manufacturing.
- Accurate representation of final prototype components.
Cons
- Often, it results in higher cost per unit in smaller production runs.
- Initial tooling cost isn’t amortized over the production of many parts.
HCR
Transfer molding is commonly featured in the manufacturing of HCR components. It’s a simple manufacturing process involving 3D printing of silicone and a viable option for rapid prototyping projects.
Manufacturers force HCR, or “gum stock” material, into heated cavities to form a part and cure it in its final form. HCR provides a natural fit for transfer molding projects because gum stock is a far more viscous material than LSR.
Pros
- Simple tooling manufacture with minimal costs involved in setup.
- Minimal process development is required.
Cons
- It’s challenging to create complex geometrical shapes.
- Extended production cycle times compared to LSR.
In Closing
Finding the right production partner is essential to the success of any prototyping project. With the right partner, you have a guarantee that your prototyping costs are low, and your components receive manufacturing with the right methods and materials.
Choose a production partner with a track record of success working with major manufacturing companies in various industries. Your production partner should offer several options for any project and cater to your timelines and custom requirements.
Silicone molding is a popular choice for rapid prototyping projects due to the durability and flexibility it offers prototype components. However, it’s not always the best choice for your prototyping project. That’s where having a top-rated production partner comes into play. They’ll recommend the right solution to match your needs.