Silicone molding is a popular manufacturing process for creating high-quality and precise products. However, ensuring that your silicone-molded product meets the desired specifications can be challenging. This article will discuss three critical strategies for achieving the best quality in silicone molding.
Choose the Right Silicone Material
The first step in ensuring the quality of your silicone molded product is to choose the suitable silicone material. Several types of silicone rubber are available on the market and selecting the one that suits your specific requirements is essential.
Different types of silicone rubber have other properties, such as flexibility, durability, and resistance to high temperatures or chemicals. Choosing a silicone material with the appropriate characteristics for the product’s intended use is essential.
Moreover, choosing suitable silicone material also involves understanding the environmental factors that could impact the performance of the molded product. For example, if the product is exposed to UV light or harsh chemicals, you must choose a silicone material that can withstand those conditions.
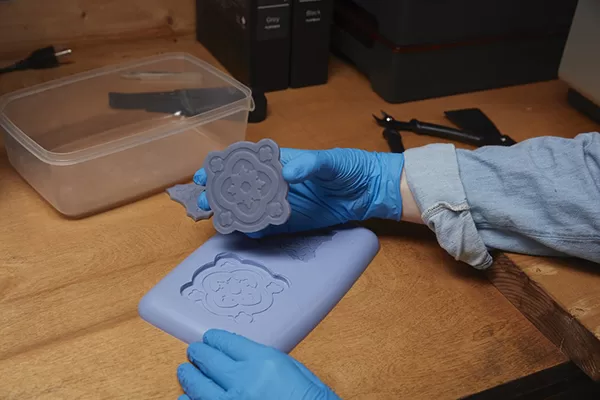
Silicone mold product
Pay Attention to the Molding Process
The silicone molding process is also critical in ensuring the quality of the final product. This includes factors such as temperature, pressure, and curing time.
Temperature is a crucial factor that affects the physical properties of silicone material. Controlling the temperature during molding is essential to achieving the desired properties, such as hardness or flexibility. Maintaining a consistent temperature throughout the process is crucial to ensure uniformity in the product.
Pressure is another critical factor in the silicone molding process. Optimizing the pressure levels in the mold to achieve the desired quality and consistency is essential. The right amount of pressure can improve the flow of silicone material, reduce defects, and enhance the quality of the final product.
Curing time is another critical aspect of the silicone molding process. The curing time determines the hardness and tensile strength of the final product. Too little or too much curing time can lead to inconsistent low-quality products.
Perform Quality Control Testing
The final step in ensuring the quality of your silicone molded product is to perform quality control testing. This includes visual inspection and technical tests, such as hardness or tensile strength testing.
Visual inspection involves examining the physical properties of the silicone-molded product, such as its shape, texture, and color. This can help identify defects or inconsistencies in the product, such as air bubbles, warping, or uneven surfaces.
Technical tests can provide more objective measures of the quality of the product. For example, hardness testing can measure the product’s resistance to indentation or deformation. Tensile strength testing can calculate the maximum stress a product can withstand before breaking.
Regular quality control testing can help ensure the final product meets the desired specifications and performs well in the field.
Final Thoughts
Silicone molding is a valuable manufacturing process for creating high-quality products. By choosing the right silicone material, paying attention to the molding process, and performing quality control testing, achieving the best quality in silicone molding is possible. These strategies will help you produce consistent and precise silicone molded products that meet the highest quality and performance standards.