You’re hunting for a resin mold to get something done quickly and efficiently. You can’t go wrong with silicone as your primary material. Silicone’s flexibility adapts to all materials you may want to mix it. You create molds from plaster from the ground up. Then you can add silicone to the mix to tamper with the properties of the finished parts to your liking. The best part is that anything with silicone naturally becomes non-stick.
If you want to create resin molds with no seam lines, you can knead some polymer clay before pressing it into the mold. There are a lot of workarounds to this procedure. The final goal of these solutions is to achieve a good level of flexibility in your project, especially if production is moving forward while you’re still in the design phase. The following are some of the best tips you can follow to get a state-of-the-art cast:
Fill the resin mold using small pieces of clay. Make sure to drop them one at a time and push down the polymer so it can reach every single crevice of the mold. Keep going with this process until the mold is filled.
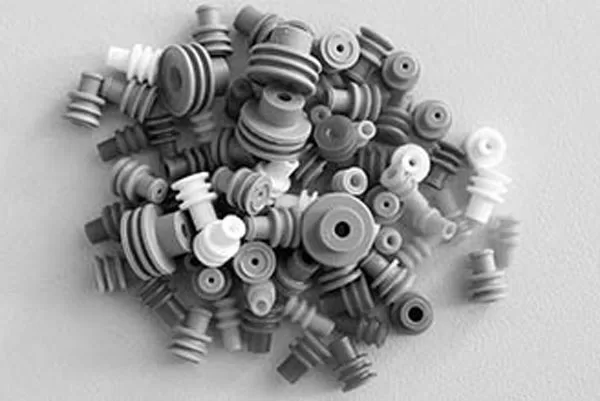
Silicone rubber parts
After filling every space of the resin mold, you can press down the clay and make it take shape while molding it. If you wish for something more malleable, you can use silicone, but you’ll have to work by pouring the material inside the closed mold.
As this process is handled manually, you can retire the cast from your resin mold using a small blade. You can trim down any spill on the edges carefully, but you must also watch out for any bubbles if you use silicone.
If you use clay, ensure the finished product is refined and thoroughly adapted to the specs you’re looking for. If you use silicone, ensure there are no excess bits of material around the mold to make sure it’s pristine and ready to handle the next part.
Working with Polymer Clay and Silicone Molds
If you’re using silicone molds to work with polymer resins, the process doesn’t drift too much from what we’ve studied already. Silicone is such a clean and easygoing solution that you can use it to bake polymer clay and create as many parts as you need.
Getting something done with silicone molds is also easier to handle, especially if the curating process is done in the cold. The polymer part will not show a single dent or deformation if the curation process has gone through without problems. You can remove the piece after it’s finally done by flexing the bottom of the mold and expelling the resin part.
If you’re making something with volume and dense texture, it’s always best to let the weight of the part do the job for you to remove it from the mold. All you need to do is press the mold facing down on a glass tray or ceramic tile and press the mold firmly while lifting the edge. You’ll get your part released in o time.