Mistakes are a fact of life. We all know that and learn from them with varying degrees of success. During the many stages of designing and then manufacturing a product or prototype, it is inevitable that something might not go as planned. However, how a void the most common injection molding mistakes to ensure a speedy delivery of the perfect product?
Excellent Project Management: As we have mentioned previously, a good molding engineer and a comprehensive DFM are essential in ensuring that you start off on the right track. Communication is essential to ensure that all members of the team understand their roles and the timeframe that production is likely to take. Communication between the molding company and the customer is not any less important, to ensure that all parties are happy and there are no unexpected bills or surprises that have not been disclosed during the design stage. Failure to ensure that the design is correct from the start is almost always fatal, as it is often too expensive and time consuming to recover the project.
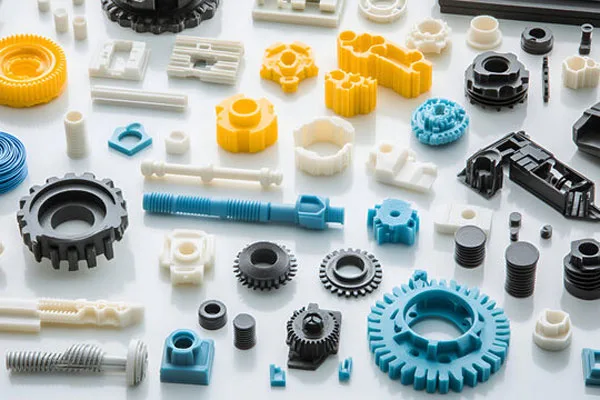
Plastic injection molded parts
Quality versus Economy: We all like to save some money, but some things are worth paying for. Listen to your design engineer’s advice regarding the choice of mold material and longevity advice and do not try and rush a project through at the expense of quality. The product represents your business and it is not worth sacrificing your reputation for the sake of a relatively small amount of money or time.
Eliminate Waste & Improve Productivity: Although this appears to be common sense, this is sometimes overlooked at the expense of speed! Rushing into a project is likely to cause product and material wastage, which may then impact the total number of items that are produced. Limited budgets sometimes cannot be stretched and the loss of a couple of hundred parts may be the difference between profit and loss.